Rotorway Scorpion Two Kit Helicopter
ARTICLE DATE: August 1978
A couple of months ago, we did a pirep on a homebuilt helicopter, the Hillman Hornet version of the Helicom Commuter helicopter. At the time, we mentioned that the Hornet was a relative newcomer on the helicopter kit scene, and that its crosstown rival, the RotorWay Scorpion helicopter, had been around for some time.
This month, we’ll take a look, not only at the Scorpion helicopter itself, but at the remarkable operation that manufactures and supports it, and the equally remarkable man in charge of the entire project, B. J. Schramm.
If there’s a single word that describes the RotorWay concept — both of building the Scorpion helicopter and of learning to build and fly it — that word would have to be “completeness.” My first visit to the RotorWay facility in Tempe, a suburb of Phoenix, Arizona, left me almost stunned with its size and complexity.
True, much of the facility, particularly the RotorWay foundry and machine shop, are not exclusively dedicated to production of Scorpion helicopter kits.
The foundry, for example, is a largely automated facility set up for the production of a wide range of rather complex castings in almost any nonferrous metal, and much of its output is subcontract work for other manufacturers—for example, electronic-equipment housings for Motorola.
Additionally, quite a bit of foundry production is devoted to RotorWay’s own specialized products, which are based on very small two-stroke engines. These include a gas-powered hand drill, ditto circular saw, “Grass Hog” weed trimmer, and so forth.
What’s important here, though, is that the manufacture of these diversified products supports the foundry— and, in fact, a large part of RotorWay as a whole—so that its services are available for the production of helicopter parts.
The same holds true for the machine shop, and the result is a helicopter kit with a staggering array of parts designed and manufactured specifically for the Scorpion helicopter, rather than bought off-the-shelf.
Thus, many of the Scorpion’s parts can be optimized for. minimum weight, where a standard part might be heavier—and the specialized parts range from tiny brackets and bushings all the way up to the engine itself, a RotorWay-designed and built 4-cylinder water-cooled 4-stroke that puts out 133 hp.
In a sense, the RotorWay factory is more like a miniaturized version of a “real” aircraft factory than a homebuilt “manufacturer.” The “real aircraft” idea is carried on into quality control and documentation.
All Rotorway Scorpion helicopter parts are logged in and out of various manufacturing and inspection steps so that each part is traceable, right back to the original lot of raw materials.
Thus, for example, if a given owner in the field finds that a certain casting is cracking, the factory can not only trace the fault and find out why it’s cracking, but can also find and notify all the other helicopter operators in the field who have a casting from the suspect lot or production run.
The actual helicopter end of RotorWay activity is concentrated in a facility called the “Sky Center,” located across a large field from the foundry and factory buildings. The Sky Center is an integral part of Mr. Schramm’s philosophy of a complete program.
Not only does it serve as a hospitality and demonstration center for prospective Scorpion builders, but it also provides classrooms in which the active builders attend construction seminars.
As part of the complete Scorpion package, builders are encouraged to come to Tempe and learn proper construction techniques, using hands-on experience on actual Scorpion parts and sub-assemblies.
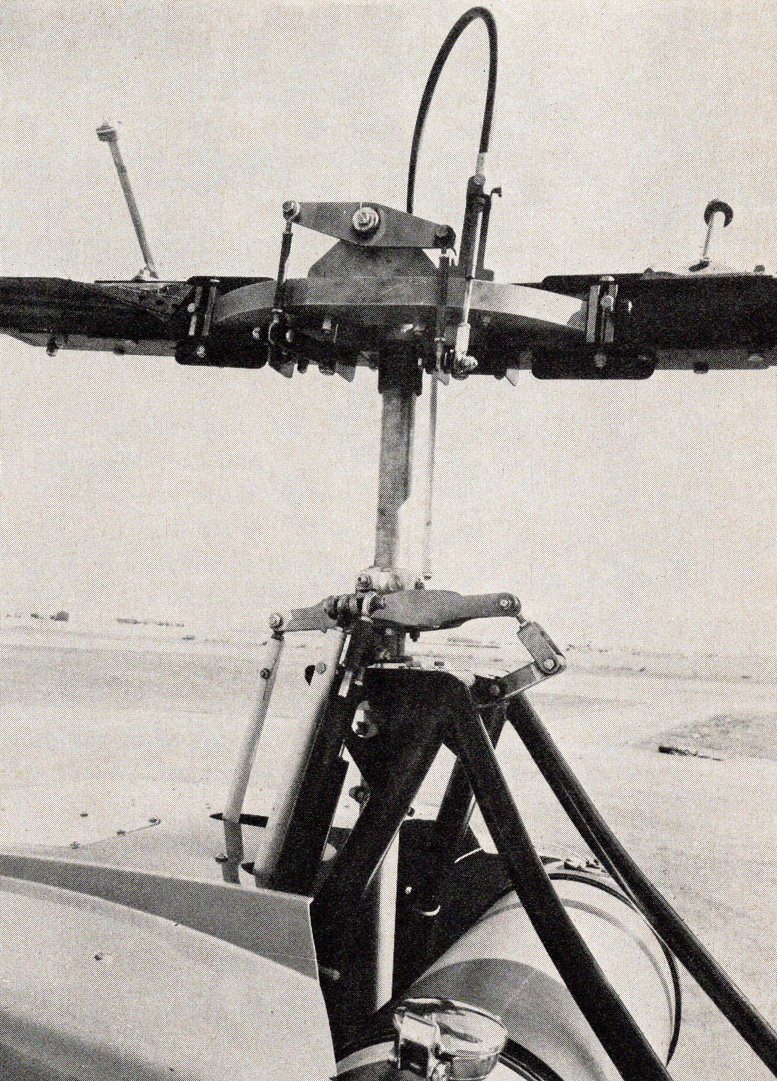
A “walking beam” arrangement transmits collective motion from the flexible cable to the blades, while the entire hub rocks for cyclic control.
They also use a library of special color video cassettes to cover certain areas. In this way, RotorWay hopes to achieve a uniform and acceptable level of construction technique and expertise, no matter how diversified the backgrounds of the builders may be.
The Sky Center also operates a fleet of Scorpions for flight training. Another part of the complete package is two separate sessions of flight training: one takes the neophyte up to and including hover solo in the Scorpion, while the second moves on into actual “up and away” flight techniques.
B. J. Schramm feels that the totality of the Scorpion package is a key to its present and future success, and that such total control — as well as almost total independence from sub-contractors for anything more complex than 4130 steel tubing, aluminum ingots, and bulk items like nuts and bolts—is essential to the design’s continued safety record (see interview).
At any rate, with minds and legs suitably numbed by the complete tour we’d received, it seemed a good time to start looking at the Scorpion itself; we acquainted ourselves with various parts of the aircraft in roughly the same order as they’d come to the homebuilder.
The basic airframe of the Scorpion is a weldment of 4130 chrome-molybdenum tubing. It consists of a central cluster which supports the engine, transmission, controls, and cabin, and a long tailboom which curves up at the aft end, hence the “Scorpion” name.
The airframe is shipped to the homebuilder with all tubing accurately pre-cut, mitered, and tack-welded at the factory.
It’s recommended that the services of an experienced welder be obtained to complete the major welding with a minimum of fuss and delay and a maximum of safety, although it can safely be assumed that at least some of the homebuilders will have had experience building other steel tube aircraft and will be able to do their own welding.
The airframe includes the skid landing gear. The major powertrain components bolt to the airframe just aft of the cabin area. The Scorpion’s transmission is a hybrid of two types: primary drive from the engine is by means of multiple V-belts, with an idler that can be disengaged and serves as a rotor engagement clutch on startup.
The large driven pulley in turn drives a sprocket-and-chain arrangement, running in an oil bath, for final gear reduction to the rotor shaft. Tail rotor drive is taken from the transmission and carried aft via long V-belts, with an idler/relay pulley halfway out the tailboom.
Smaller V-belts from the engine drive the water pump and cooling blower for the radiator. The rotor system and its controls are the next major assembly we considered; Schramm’s design uses a rather unique control system which is deserving of special mention.
The basic rotor design is a semi-rigid underslung type, with teetering and rocking hinges. A single pushrod from the cyclic swashplate transmits motion, not to pitch horns on the blades (as in, for instance, a Bell or Hornet) but directly to the rotor hub itself.
Thus, cyclic control is accomplished by rocking the entire hub, rather than by cyclic feathering of the individual blades. Collective control does use the pitch horns: a flexible Bowden cable runs up through the center of the rotor mast and turns back downward to move one blade’s pitch horn directly, while a “walking beam” arrangement reverses the direction of movement for the other blade. Thus, the only time there’s any actual movement about the rotor’s feathering hinges is when the pilot is actively moving the collective stick.
The arrangement also means that, at rest, there’s no frictional loading, and the collective feels like it’s flopping loosely; there’s no collective friction lock, either. With the rotor turning, centrifugal and aerodynamic forces snug on, up the bearings to the point at which as the collective stays put.
A look at the control systems give a good impression of the extent to which specialized parts are used.
Where the various and sundry brackets, bellcranks, and links in the controls of the average homebuilt helicopter are bandsawed from heavy stock or welded up from sheet or tube, in either case resulting in a distinctly “homebuilt” look, the control parts of the Scorpion incorporate all sorts of castings and machined parts, and is, look and feel thoroughly professional.
The collective linkage includes a correlation system to minimize required throttle-twisting. The antitorque pedals are connected to the tail rotor by means of another long flexible Bowden cable. Dual controls are optional, but are ordered on virtually all Scorpions. The heart of any helicopter is its engine, and the Scorpion’s RW 133 engine is one of its most impressive features.
Until a year or so ago, Scorpions were equipped with two-stroke, water-cooled Evinrude V-4s, originally developed as the powerheads of big outboards. These were the only engines offering the required power-to-weight ratio with an acceptable degree of reliability.
Since then, though, Schramm and his cohorts have developed their own engine—again, only possible for a firm having access to the kind of sophisticated foundry and machining capabilities that RotorWay has.
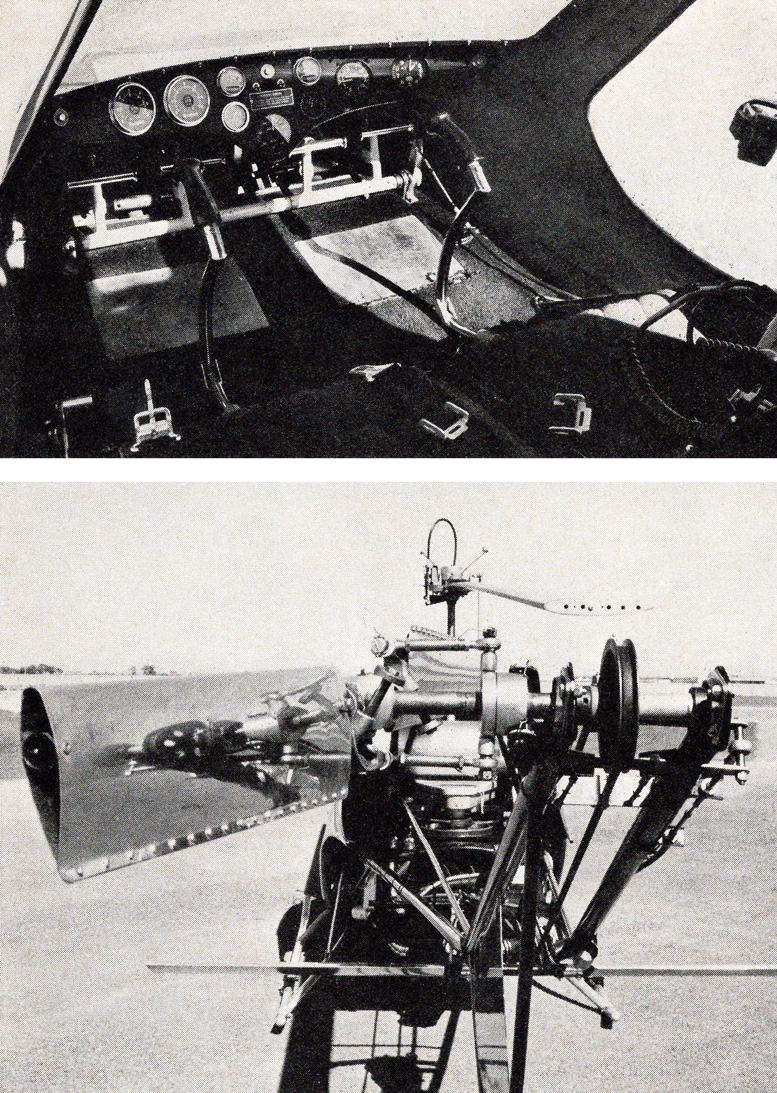
V-belts are used to drive the Scorpion tail rotor.
The RW 133 has a displacement of 133 cu. in., and puts out an impressive one horsepower per cubic inch, a volumetric efficiency quite rare in an engine this small. Output shaft speed is 4500 rpm, much higher than that of an airplane engine but perfectly acceptable for a helicopter, which requires elaborate reduction gearing (or belting) in any case.
In fact, the high engine speed is necessary for good efficiency; other contributing factors include the water cooling, which allows safe use of high compression and its attendant high combustion temperatures, and tuned intake and exhaust manifolds.
For those who plan operations at high altitudes and/or hot weather, a turbo charger is available as an option. The engine is built almost entirely at the Rotorway factory; in fact, virtually all of its parts are produced from scratch right on site, including very elaborate castings for such parts as the water jackets and crankcase.
Even ferrous-metal parts such as crankshafts, which cannot be cast in the foundry, are forged by a sub-contractor and shipped in a rough state to Rotorway for actual machining.
Prior to shipment, each engine is run in a dyno which is, for all practical purposes, a truncated Scorpion, so the customer can be sure that it will meet specs in his actual installation. The cabin enclosure is supplied by RotorWay in the form of laid-up fiberglass shells.
The rear section contains the seat pans as an integral part; the windshield must be mounted at a fairly precise angle on the forward section, since airflow over it in forward flight influences the trim of the helicopter. The cabin shell is whitish, with final choice of color up to the homebuilder. B. J. Schramm himself was my pilot and mentor for a brief demonstration flight.
Normally, no one gets to fly the Scorpion without going through the whole flight training program, regardless of prior experience, but for this occasion he consented to install the right-seat cyclic, although the only collective on this particular ship was the one on his side.
One of Schramm’s concepts, and one of the rationales behind his elaborate training and construction programs, is that the Scorpion pilot will know enough about his ship to be his own mechanic—and, of course, will be familiar enough with his bird so that he can feel when something’s in need of adjustment.
Sure enough, when we got into the snug little cabin, B. J. stirred the cyclic about a bit, decided that it was a little too stiff in the fore-aft direction, produced a wrench, and reduced the friction in one of the torque links at the swashplate. This reduced cyclic friction to its normal level — of none at all with the rotor at rest.
The collective, of course, feels similarly “disconnected” until the blades start turning. Like most highly-tuned engines, the RW 133 seemed to need a bit of tickling and prodding before finally starting; once running it settled down to an idle that impressed me with its smoothness and quiet.
Of course, water-cooled engines, with their thick water jackets and no fins to radiate noise as well as heat, are inherently quieter than air-cooled types; exhaust noise was also quite low, and should be even less in the turbocharged version.
A good-sized handle to the left of the pilot’s seat engages the V-belt idler and gets things in motion at the top of the rotor mast; with the rotor up to speed and the separate engine and rotor tachometers indicating the right values, the throttle can be cut to “split the needles” and make sure the overrun clutch is working properly.
There’s no mag check, since the engine uses single ignition; according to Schramm, with the RW 133’s — small displacement and high compression ratio and speed, this is entirely sufficient.
B. J. made ,the takeoff, climbed to a cruise altitude of about 500 feet above ground, and got things generally squared away before he let me try my hand at the controls, and I can see why RotorWay usually makes sure that anyone planning to fly the Scorpion gets some dual instruction and/or tethered hover practice first.
I found the controls very responsive to even the slightest movement; at the same time, the combination of high rotor speed, low disc loading, and the “flying hub” control system make the helicopter feel a bit different, at least to me, from even the lightweight Hughes or the little Brantly in which I got my CFI-H.
I found myself tending to over-control, with pitch attitude wandering quite a bit, although things felt a bit better after a few minutes.
I also found myself a bit disoriented by the lack of a collective on my side; I’m just not use to not having anything to do with my left hand, and I’m sure this contributed to a certain level of tension and unfamiliarity which can’t have helped my helicopter skills, such as they are.
(Of course, all the ships used at RotorWay for actual dual instruction have complete dual controls; the ship we were flying was B.J.’s own “pet helicopter.”)
On our way back to the Sky Center’s grass-lined practice area, B.J. demonstrated an autorotation. What with the light disc loading, the Scorpion doesn’t come down too terribly fast, which is nice, but the same factor causes it to shed rpm pretty quickly when the power is cut.
Of course, the rpm comes back equally quickly in the flare, but there’s not too much blade inertia, so the flare itself struck me as quite rapid, with a considerably more pronounced nose-up angle than I’m used to from production helicopters. We used a power recovery, so I can’t say how gently the ship will set down from an auto.
We then returned to the pad, making an approach to a spot some 100 feet short of the pad and hovering up to it in ground effect. I tried my luck at a hover, and again found the little helicopter quite a handful.
While V could note increasing familiarity and improvement even in the 5 minutes or so we spent in the hover, I still had that “balancing on a beach ball in the deep end of the pool” feeling that I recall from my student days.
The rule in helicopters that “the bigger they are, the easier to handle” seems well borne out in the Scorpion. Even so, I’m favorably impressed, pot only by the aircraft but especially by the program under which it’s manufactured, distributed and supported.
The program is unique in aviation, and it will be interesting to watch its current and future progress. The kit is unbelievably complete, and while the price tag of $13,500 seems a bit steep at first glance, let us not forget that this is the era of the $5,000 Volkswagen!
I’m looking forward to the chance to fly a Scorpion enough to become reasonably proficient in the thing, at which time we’ll do a follow-up pilot impression; we’ll also try to fly one or two owner-built birds, rather than just the factory ships.
In the meantime, suffice it to say that it’s a remarkably sophisticated helicopter, especially for a homebuilt, produced by a sophisticated firm in a sophisticated program—and for the ambitious homebuilder, it can offer a unique, *ancf sophisticated, reward.”
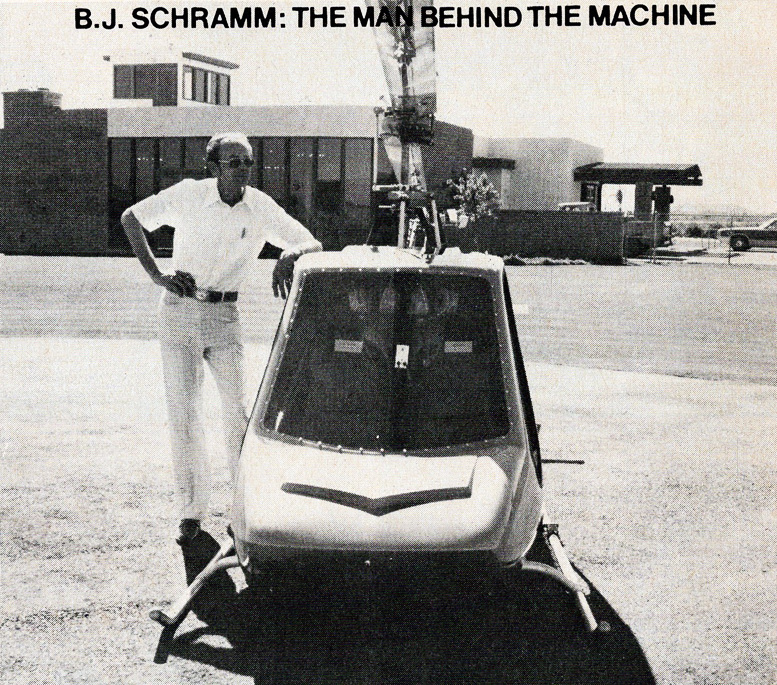
B. J. Schramm and the Scorpion. Now, the big question: will he fit inside?
As the dean of the homebuilt-helicopter entrepreneurs — in fact as the first person to successfully develop and market a homebuilt chopper — B. J. Schramm has a lot to say. He’s an impressive figure even if considered only in light of the Scorpion, not to mention his founding and developing RotorWay as a whole.
When we went to visit RotorWay, we soon found that our interview with Mr. Schramm went far beyond the confines of the Scorpion, ranging out into the underlying philosophy of the aircraft business as a whole.
Here, though, are a few excerpts that apply directly to the Scorpion:
Schramm: . . . the people that are spending money now on Cessna 152s will, in the next few years, be thinking very seriously about spending that money op RotorWay products.
Question: So you feel that your market is presently buying fixed-wing airplanes?
Schramm: A good portion of it is. In the recreational area per say and I would say we have been 80% recreational in the past. We’re getting more and more utilitarian, and I think you’ll see that when you analyze the ship a bit closer.
In the future, if we are going to be successful on a numbers game basis, we are then going to have to become more utilitarian, and as we approach that utilitarian market, we are going to have to begin to compete, in a sense, with the people that are out there buying fixed wings now . . . let’s face it, we aren’t going to sell helicopters like recreational vehicles.
Question: Do you see yourself developing to the point of producing a manufactured helicopter, as opposed to a kit?
Schramm: Well, we haven’t begun to scratch the surface of the market in the amateur-built category yet.
Question: Legally, for example, don’t you think there are limits as to how utilitarian you can become? Artificial limits that are constrained upon you by the experimental type certificate?
Schramm: Not in the helicopter area. We have had our helicopters operate in the same areas, other than densely populated areas, that any other helicopters do.
W 133
Question: Yes, but they can’t operate for hire – true?
Schramm: That is correct. In some countries they cannot be used for financial gains, meaning they are pure pleasure craft – not to be operated for paid work like paying someone to muster cattle or spray fields. BUT! technically, you can do this yourself as the owner operator of your helicopter.
Question: And they can’t operate to give required flight training?
Schramm: No. But how many businessmen use their Cessna 152s for hire? They’re using them for their own business. You can use this ship for your own purposes.
Question: You can use an experimental aircraft in the furtherance of your own personal ventures, but you can’t hire it out to someone else?
Schramm: That’s right.
Question: Let’s say I’m a surveyor, because here is an ideal application . . . I hop in my Scorpion and buzz off to a hilltop and put down my corner reflector, and then I fly to another hilltop and take a shot at it. And then I charge the people I do this for an arm and a leg. And I’m not going to run into problems from the Feds?
Schramm: No, this is in your own business. As a farmer, you could fly out over your land every day and see where the water spots are and where you want to put more fertilizer, and that’s your own business.
Question: If that’s not a limitation, then certainly there’s a limitation in that whoever wants to use your product has to assemble it.
Schramm: Oh, yes, and we like that because we don’t think that anyone should become involved with the Scorpion unless they have some mechanical capability, unless they are prepared to work on the ship themselves.
Question: Tell us some more about the power plant.
Schramm: Well, first of all, I think we could say that any aircraft is the power plant, it’s that important. Without the power plant, you don’t have much of an aircraft. We are dealing, here in the helicopter area, with a very specialized piece of equipment . . . if we go to a 125 or 150 hp Lycoming, we’re dealing with a 300-400 pound engine.
That means that if we’re going to build a reliable helicopter, we’re going to build the same size helicopter that Hughes has in the 269 or 300. Now, if we build that size ship, we’re competing with them! So we couldn’t; we found that we had to have a specially tailored power plant.
You can’t build your power plant until you have your own pattern-making facilities, foundry, tool and die shops, and your own in – house machining capability. You’ve got to have an engine factory.
Question: What are some of the problems you’ve come up with?
Schramm: What we’ve done, in dealing With the market, is that we have learned over a period of years — and we’re still learning—how to communicate this miserable mass of vibrating motion to Mr. John Q. Public in a palatable way he can understand.
This is a big task We started out with conventional plans, three-view drawings, pictures and numbers like everybody else did, and have evolved into a much more advanced system.
Question: Advanced in what way?
Schramm: At the present, the program that we use is called “See-Do.” Our manuals are based on this type of format . . . receiving inspiration from Popular Science Magazine’s concept of the “Wordless Workshop.”
RotorWay has developed a form of pictorial presentation which strongly emphasizes the belief that a picture saves many words. The goal of this system is to break a job down into a series of simplified steps providing a procedural path through what may have initially appeared to have been a difficult task.
Question: How long does it take, on the average and for the average person, to assemble a Scorpion?
Schramm: Well, these times have been changing as the years go by, because our program of instructions has been improved, and the quality control and fit of our parts has also improved.
I would say that a person could get a ship together now in about a 6 to 8 month period, if he put some effort into it. At this point, our average construction time is around a year and probably going down. It was up around a year and a half.

Buy this helicopter kit and RotorWay will teach you to fly it . . . after they teach you to build it.
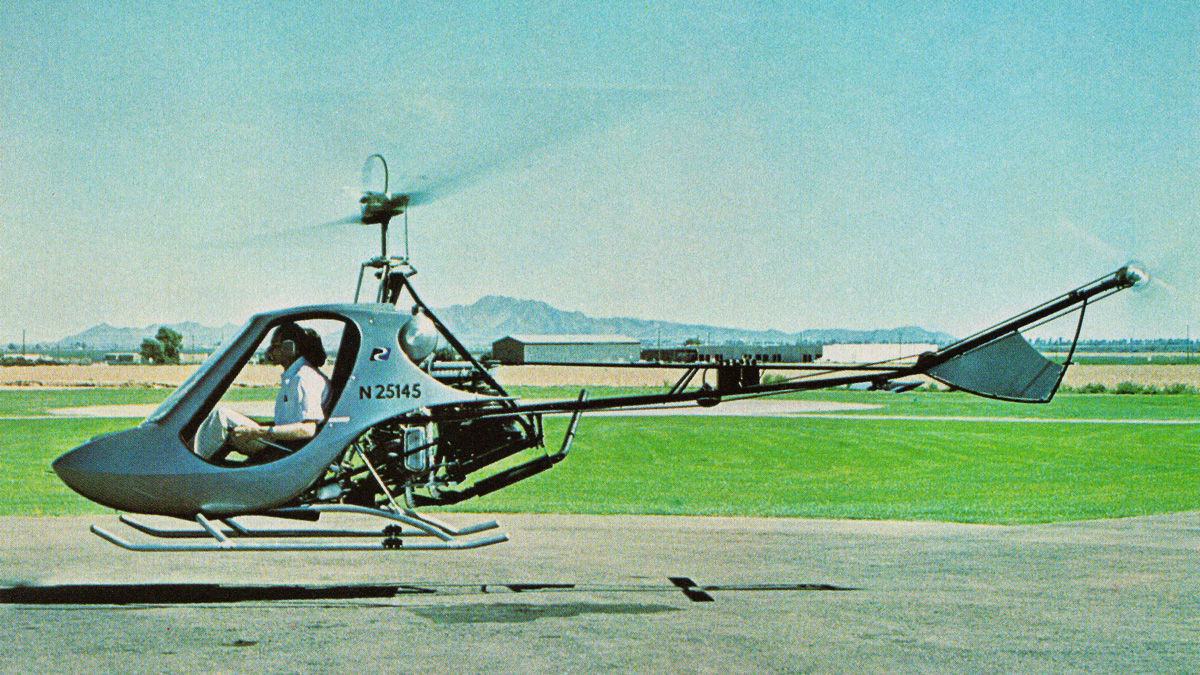
i want to buy one kit.