Extruded Aluminum Rotorblades
The purpose of this helicopter rotorblade article is to review two flight applications and provide some insight into using the unique untwisted, constant chord series of Vortech International, Inc. (VII) extruded 6063-T6 aluminum rotor blades. These two flight projects are the Skytwister helicopter, built by Ben Showers and the PAM 100B Individual Lifting Vehicle (ILV) or “flying platform.” Ben’s Skytwister has accumulated approximately 100 flight hours at speeds up to 70 knots; the PAM 100B has many run hours at blade rotational speeds up to 1300 RPM.
First, just a few words about the extruded rotor blade system itself. There are several advantages to this system: a surface free of major imperfections such as rivets or seams, blade lengths easily tailored to the home builder’s individual requirements, availability in two airfoil selections (symmetrical NACA 0012 and asymmetrical 8H12) and a number of blade chord sizes ranging from 2 3/4″ to 8.” The smaller size can be used for helicopter tail rotor blades.
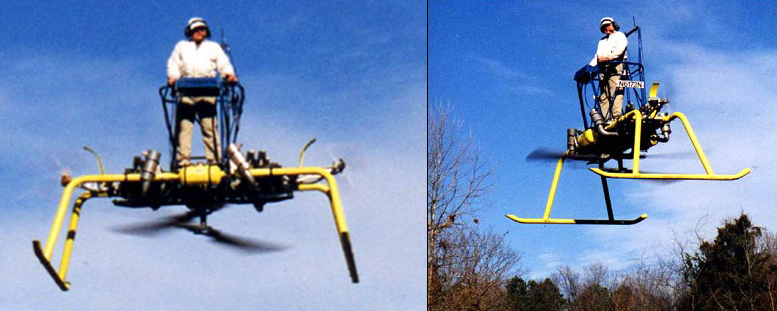
Individual lifting vehicle drone helicopter platform
Secondly, there are several general areas that have to be addressed when building anything as important as a rotor blade. Care must be used when looking at the finish, blade balance and the strength of the root hub connection. Since the blades are supplied with a “mill” finish; it is recommended that the blade surface be initially worked with a light abrasive such as Scotchbrite to prepare the surface and then use standard aluminum polishing techniques to provide a bright, long-lasting, weatherproof finish. Painting or anodizing is not advised.
A full length 6061-T6 aluminum nose weight (for strengthening and balancing the system) is provided as part of the blade kit (along with plastic tip and root caps and grip plates). Balancing each blade both chord-wise and span-wise is VERY important. Span-wise balance must be done for each blade set or in-plane vibration will result, its severity depending on the rotor RPM and degree of imbalance.
Chord-wise imbalance (C.G. should be 25% of chord for a symmetrical airfoil) on any rotor blade will result in higher collective and cyclic loads for helicopters. It may also result in rotor blade flutter, the severity of this condition becomes particularly noticeable with helicopters at high forward speed and increasing values of disk loading and lower values of blade collective torsional rigidity.
The Skytwister helicopter rotorblade uses a 7″ chord blade, has excellent handling qualities and has not experienced flutter throughout the entire flight regime. The disk loading is a low 1.7 psf, however. The chord-wise balance point for the basic symmetrical airfoil is 41.6% with no nose weight.
If the standard aluminum nose weight is used, the balance point is brought to 30.7%. This is what the PAM-100B uses (ground adjustable pitch only). If a 1/2″ groove is machined from the nose of the aluminum leading edge weight and a brass rod is inserted, the balance point is then a very respectable 26.6%.

Experimental flying platform
The optimum method to chord-wise balance the helicopter rotorblade is to evenly distribute the weight along the entire span. Ben has great success, however, using an externally adjusted root weight (see Skytwister hub photo) which he can trim so that the collective does not move at any pitch setting. Blade attachment to the hub is another very important item. This is best accomplished by looking at what others have successfully done or contacting someone with experience in the design of rotor hubs.
As with any large rotating system, great care must be observed when machining the attachment holes in the blades. They must be accurately drilled to allow the blades to properly align and have no play in the holes when the retaining bolts are inserted. See the pictures of the mounting methods used in these two projects.
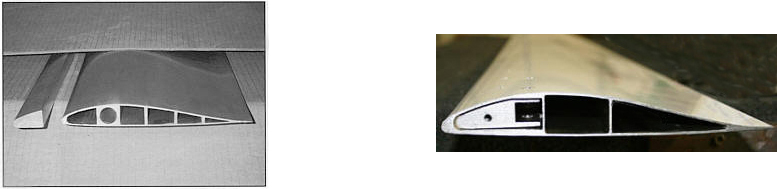
Helicopter rotorblade profile – both 8-H-12 (shown) and NACA 0012 are available.
The VII rotor blade system is accumulating a record of testing and analysis in addition to the operational experience. Through experimental testing, the torsional twisting coefficients have been determined; the blade cross-sectional area moments of inertia have been calculated and also experimentally verified. These mathematical expressions are important when determining the strength, bending moments, and dynamic characteristics of the blade.
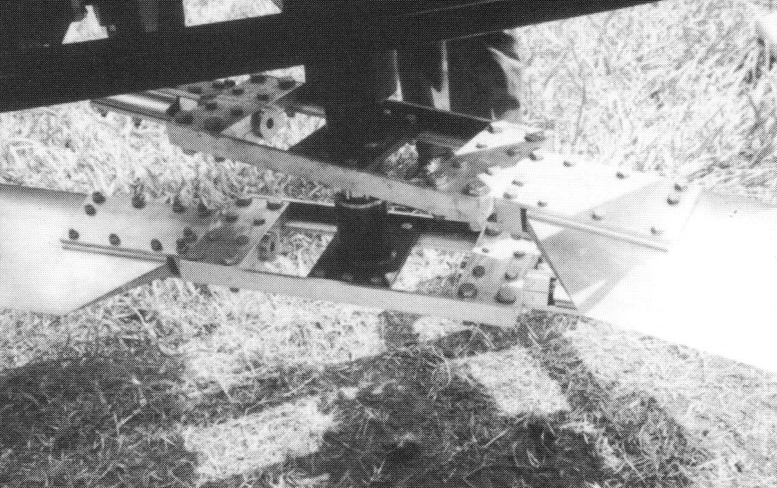
PAM 1000B flying platform extruded blades
The PAM Group has also statically tensile-tested their rotor system (including an 8″ symmetrical section of the VII blade) up to 35,000 pounds with no adverse effects to the blade section. In addition to the experimental work, several fatigue analyses have been made that show, under normal operating conditions, an extruded aluminum helicopter rotorblade life in excess of a thousand hours depending on the particular application. Both Ben and the PAM Group have found that the extruded blade system is a very durable one that can withstand a great deal of abuse and still perform.
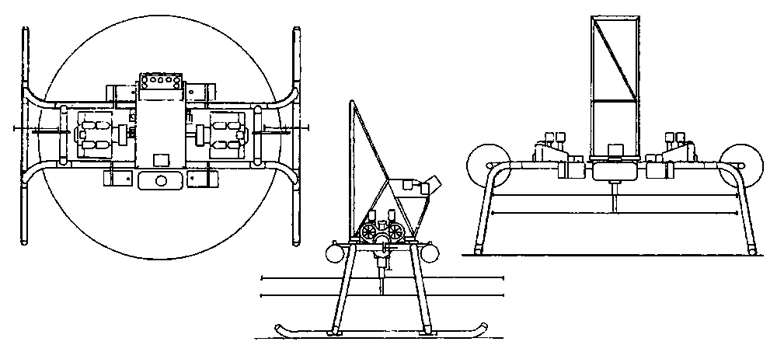
PAM 1000B flying platform
The rotorblades are still available from Vortech. There have been some changes to the rotor blade design and materials since this article was written, so it’s best to check with the manufacturer for details.
Be the first to comment on "Extruded Aluminum Helicopter Rotorblade Review"