Rotorway Kit Built Helicopter Evolves
Introducing The Upgraded Exec 90: a chopper for the 1990’s.
ARTICLE DATE: January 1992
I flew the Rotorway Exec kit helicopter for the first time in 1984 for a story. Back then, I had no helicopter rating, no helicopter time and essentially no knowledge of what makes rotary wing machines tick…or whirl. My first assignment was to keep the chopper at a consistent altitude in the vicinity of the huge training pads.
I couldn’t do it. I was all over the field. I couldn’t hold altitude, heading, position or speed for more than two seconds at a time. The machine became friendlier after about three days and six flight hours, and I eventually learned to pick up the Exec and hover in place with a semblance of control.
I returned to Phoenix recently to fly the new Exec 90 helicopter, the latest version of the machine, dramatically revised and upgraded for the ’90s (thus the new designation). In the half-dozen years since my introduction to helicopters, Rotorway has been sold and reorganized by new owner John Netherwood.
He built the first Exec in Britain, retired from the forklift business and became Rotorway’s British dealer, mostly for fun. When Rotorway ran into financial problems early last year and filed bankruptcy, Netherwood jumped at the opportunity to acquire the company and closed the deal in April of 1990, naming the new company Rotorway International.
Though the Exec always was one of the better looking helicopters, and that has only changed for the better, Netherwood had his own ideas about what needed fixing on the aircraft.
He felt the people who knew the Exec best, a dozen of Rotorway Aircraft’s designers and engineers, might have even better insight. They did, and the 18 changes that produced the Exec 90 are primarily a result of their input.
Since the Exec 90 is the only two-place homebuilt helicopter on the market, it’s probably only fair that it uses its own engine, manufactured specifically for the aircraft. B. J. Schramm, designer of the Exec and the Scorpion before that, was the originator of the first 133-cubic-inch Rotorway engine back in the mid-’70s.
The engine was progressively improved and upgraded to 162 cubic inches; then, granted a new water jacket, new heads and sodium-filled exhaust valves.
The latest version is designated the RI162 and rated for 150 hp at 4250 engine rpm. Channeled through an eight-to-one reduction gearing system, the main rotor turns at about 520 rpm at red-line.
With a 25-foot diameter blade chopping up the sky overhead, the rotor is generating tip speeds of about 404 knots or Mach .61, resulting in relatively quiet flight (for a kit helicopter).
What makes the RI162 engine unusual is that it’s water-cooled. Liquid cooling can be a definite advantage on those missions that demand extended hovering, since cooling is less dependent upon airflow across the cylinders.
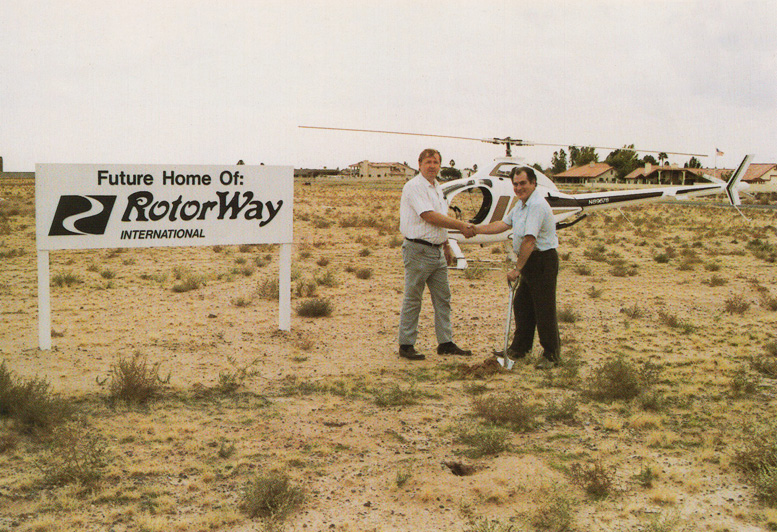
NEW FACILITY BUILT FOR ROTORWAY INTERNATIONAL – Ground has been broken and the new home of RotorWay International is under construction. The facility is being built at Stellar Airpark in Chandler, Arizona. Comprising 37,000 square feet, it is scheduled to be completed in May 1993, at a total cost of $1.5 million. Currently in four different locations across the valley, the new building will enable RotorWay to house all of its departments, including the fight and engineering school, under one roof. This will not only allow for increased production (currently at two helicopters with RotorWay engine per week) but will reduce operating costs considerably. “The new facility will allow us to take our customers through the complete manufacturing process of an Exec 90 helicopter kit, from airframe welding to engine assembly, right through to the final crafting. Then they can step out the door and into the finished product for a flight,” said RotorWay President John Netherwood. “Of course we do not actually need the runway, but it will be useful for some of our customers!” RotorWay International has sold 200 Exec 90 kits over the past two years, over 100 of which are now flying. With the new Quick Kit Option cutting the build time to 250 hours, this number is rapidly increasing.
Since you asked, TBO on the RI162 is 1000 hours, with a top overhaul recommended at 500 hours, and those are probably fairly realistic figures, if lower than you might expect of an aircraft engine.
Remember, however, that helicopter stage lengths typically are far shorter than those of fixed-wing machines, so time doesn’t build up as quickly. With only 17 gallons capacity and a burn rate of about 8 gph, you couldn’t safely fly much over two hours anyway, and the majority of helicopter flights are considerably shorter than that.
Under these guidelines, 150 hours a year would be high utilization. As partial compensation for the Rotorway’s reduced TBO, overhauls are somewhat less expensive than most pilots are used to with similar horsepower Lycommings and Continentals.
A typical top performed by Rotorway International runs about $900. A full-blown overhaul costs roughly $4,000. (In contrast, the Lycoming 0-320-B2C installed in the R22 costs $9,000 to overhaul, though it is rated for 2000 hours between overhauls.) Netherwood made a number of other significant changes in creating the Exec 90 kit helicopter.
Tail-skins and rotor blades were upgraded from .020- to .025-inch aluminum to improve tail rotor life. (The old tail rotors were rated for only about 250 hours, and Rotorway International believes the new blades will last twice that long.)
The main rotorshaft was lengthened and thickened, adding both strength and smoothness and contributing to performance. Main rotor TBO is 500 hours. A new landing gear was designed to distribute landing loads more evenly and to accommodate a skid weight that could be positioned for solo flying to off-set the weight of the right seat passenger.
For a variety of aerodynamic reasons, light helicopters often suffer from lateral CG problems. On the old Exec, things were fine as long as you always operated solo or always flew with a passenger. Re configuring from solo to a passenger or vice versa was a true pain.
It was necessary to reposition the battery and add weight on the right side to maintain a proper lateral CG in order to fly solo. To switch from dual to solo on the Exec 90, the pilot merely moves a 25-pound weight from a mounting stub just aft of the engine to the tip of the right skid.
Other improvements to the Exec 90 include a revised fiberglass doghouse (the fairing surrounding the rotor shaft), eyebrow windows above the cabin, a modernized cyclic with buttons for starter, intercom and transmitter, an overhead switching console, a dual rotor/engine tachometer and other small changes to round out the upgrade.
I flew the new Exec 90 from Stellar Airpark south of Phoenix near the four-acre site of Rotorway’s future manufacturing and corporate headquarters.
This time around, flying the Exec 90 was pure joy. Like most helicopter students these days, I earned my rating in a Robinson R22, an excellent trainer and one of the most sensitive small helicopters on the market, so the Exec 90’s quick control response made me feel right at home.
Long ago, when I was working toward my instrument rating, my instructor coached me to think of control inputs as pressure rather than movement, and that system works just fine on the Exec 90.
If you’re too bold on the cyclic or collective, you almost inevitably over-control. The helicopter is so responsive, it’s almost psychic. It seems to translate the mere thought of a maneuver into action—something like a non-aerobatic, rotary wing Pitts SIS.
Personally, I’ve always been something of a control freak in aircraft of all descriptions, so the lighter the touch the better. Hovering in an Exec 90 is simple once you get the hang of letting your fingers do the flying rather than using your whole arm and once you learn which anti-torque pedal to push.
Since he’s used to driving on the left in England, John Netherwood is probably delighted that his Exec 90’s main rotor rotates the “wrong way,” clockwise rather than counterclockwise like the Robinson R22 and other American helicopters.
In practice, the difference is moot. Some aerodynamic forces must be countered with opposite pedal, but the adjustment during liftoff, hovering and translation to forward flight is virtually automatic.
Gross weight on the Exec 90 is listed at 1425 pounds, and since a typical empty weight runs about 925 pounds, you’ll be left with a useful load of around 500 pounds. Subtract fuel weight (110 pounds) and the helicopter can legally carry a substantial 390 pounds of people and things.
That’s a pair of 190 pounders plus a camera bag, more than most two-place fixed-wing machines can handle. As it turns out, the Exec 90 lifts the weight well. Climb performance is good, certainly better than you’d expect from a comparably-powered fixed-wing airplane.
Count on about 1000 fpm from sea level under ideal conditions at 50 to 60 mph. In the real world of worse than standard conditions, that means you’ll normally experience 700 to 800 fpm with a full load and rarely need to climb for longer than four or five minutes.
Speed and altitude don’t mean as much to a helicopter pilot as to an airplane pilot. A helicopter is in its element at comparatively low altitudes, and for that reason, truly high altitude performance isn’t particularly relevant.
The ability to hover in high terrain can be an important consideration, however, especially if you live in the Mountain West. The Exec 90 can hover in ground effect (inevitably abbreviated HIGE) at a 7000-foot density altitude, and out of ground effect (HOGE) at 5000 feet.
In other words, like most small, non-turbocharged helicopters, the Exec 90 isn’t in its element at places such as Denver, El Paso or Albuquerque in the summer when density altitudes often soar to five-figure heights.
The kit helicopter can still operate at reduced weights up high or in situations that don’t demand extensive hovering. Service ceiling is listed as 10,000 feet, in case anyone cares to fly high.
A helicopter’s greatest utility comes in its ability to operate independent of airports on short legs, so blazing speed isn’t a prerequisite. That’s not to suggest the Exec 90’s near-100 mph cruise isn’t gratifying.
Level at 500 feet above the desert with power two inches below max, I saw indicated airspeeds nudging 100, and vibration wasn’t excessive. All light helicopters manifest some low frequency vibration at high speeds. In sideways or backwards flight, the Exec 90 is limited to 20 mph.
Like all helicopters, the Exec 90 is best operated with due respect for altitude and airspeed limitations. On the Exec 90, a safe autorotation is possible at zero airspeed from 500 feet AGL or from 60 feet at 60 knots forward airspeed.
These limits are defined in a chart called the height/velocity envelope, and flight inside the shaded portion of that envelope isn’t recommended. In the event of a power failure in this envelope, the helicopter will lose lift and react similar to a fully stalled airplane.
The whole idea of vertical flight is that helicopters can do what most airplanes can’t, operate low and slow or low and stopped, but all helicopter pilots accept that their machines aren’t foolproof. Normal landings in the Exec 90 start with an approach at 65 mph, followed by a gradual deceleration and descent to maintain a flight profile outside the height/velocity limits.
The concept is similar to staying within gliding distance of the airport in a fixed wing. My flight with Stretch Wolter included a little of everything—steep approaches, autorotations, confined areas—and the Exec 90 acquitted itself admirably despite my amateurish technique.
The Exec 90 kit sells for $42,500, and that includes the RI162 engine, the elastomeric rotor head, a complete main rotor, dual controls, engine instruments, upholstery and virtually everything else you’ll need to wind up with a flyable helicopter.
Once you take delivery of the total kit, Rotorway suggests a first-time kit helicopter builder can expect to spend about 500 hours in the assembly process. Building an Exec 90 is mostly a matter of assembling components, though some welding is required so there’s also a little fabrication involved.
Apparently, the process isn’t too intimidating, as some 1000 kits have already been sold, and best estimates suggest at least 300 Execs are flying worldwide. At this writing, only four Exec 90s are in the air, but there should be nearly a dozen in the air by the end of 1991.
BUILDERS TIPS
Many homebuilts have no thick walls through which to route wiring.
For that matter around the windshield bow and in the cabin area it is difficult to find a way to run wires up to the cabin light, beacon and so forth in a manner that is inoffensive to the eye. The sketch shows one way you can handle the job.
The best part of this method is that the wiring can be inserted or removed without removing the windshield, tape or the plastic tubes.
The short sections of plastic tubing can be taped on the windshield side and hidden from view to the pilot or passenger.
SMOOTHING OUT THE SYSTEM
ARTICLE DATE: September 1994
To aid builders of RotorWay helicopters in adjusting their rotor system, the factory has introduced a Reflex Trailing Edge Fixture. “A carefully balanced rotor system is of the utmost importance,” said John Netherwood, President of RotorWay International.
“It will not only increase the helicopter’s performance but, at the same time, will reduce wear on components.” For those not familiar with helicopters, a balanced rotor system is one in which both blades pass through exactly the same air.
For this to happen on RotorWay’s asymmetrical rotor type-rated in the primary class in Poland, this popular homebuilt is very close to receiving certification in Australia, a high potential market for an amateur-built helicopter. For more information on RotorWay and their new Reflex Trailing Edge Fixture, contact RotorWay International.
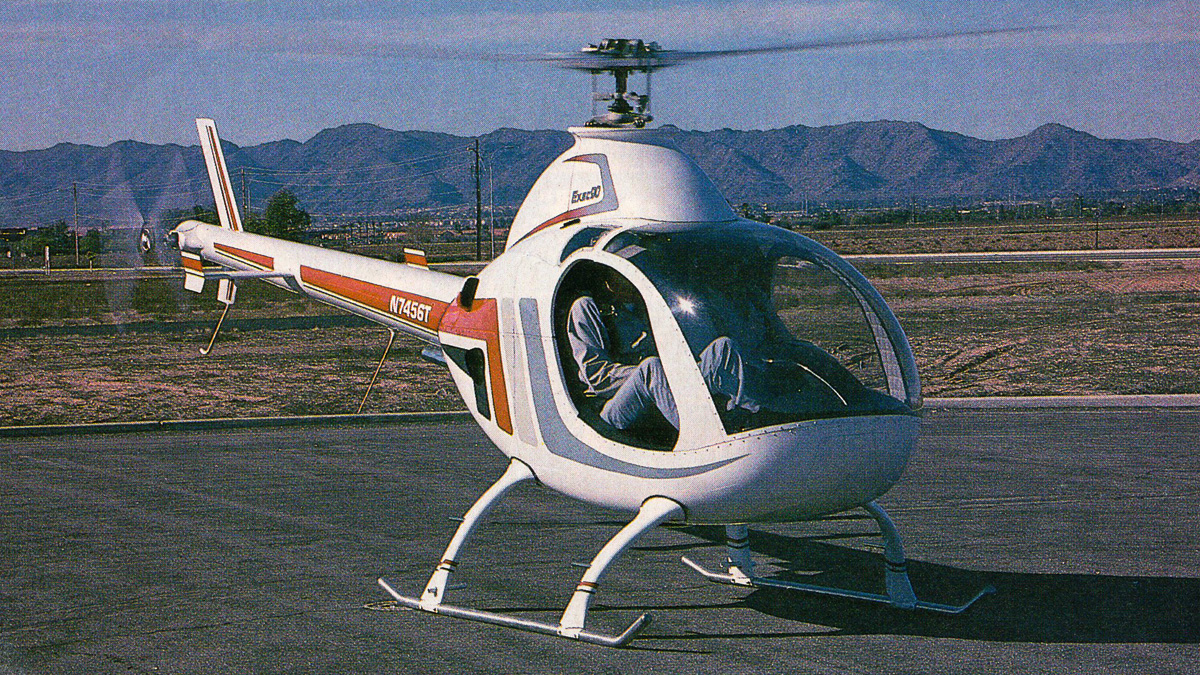
Be the first to comment on "Executive Class Kit Helicopter"