The Rotorway Helicopter Companies Executive Decision
ARTICLE DATE: AUGUST 1989
RotorWay’s Exec isn’t just the only homebuilt helicopter kit available — it’s one of the most sophisticated and complete kit programs for any homebuilt aircraft
When you consider how massive a project almost any homebuilt aircraft can become, the prospect of a homebuilt helicopter can become daunting indeed – even if it is the Rotorway Helicopters Executive helicopter.
After all, even today’s exceedingly complete superkits for some of the composite high-performance two-place fixed-wing airplanes can require anywhere from 1000 to 3000 hours of work to complete, and in some ways they’re much simpler than a helicopter.
Some times I wonder whether prospective kitbuilders realize how much work that is: If you’re employed full-time, with two weeks vacation, you’re putting in only 2000 hours a year.
If you’re a really conscientious homebuilder, you might be able to put in up to 25 hours a week; that’s still sixty weeks — a year and two months — of unremitting work. Now think of how much more complex that might be if you were building a helicopter.
Not only do you have to build an air frame, but you have to install and align myriads of rotating dynamic components, and the whole thing has to be precisely balanced or it’ll try to thrash itself apart. Isn’t that why commercial helicopters cost so much? I mean, look at that rotor head — it’s like a Swiss watch!
These thoughts are the conventional way of looking at the idea of a homebuilt helicopter project, but if you look a little deeper, you’ll find that it ain’t necessarily so.
An affordable and attainable homebuilt helicopter is, in fact, within the reach of quite a few would-be owners and pilots, and this is due almost entirely to the efforts of one man, B. J. Schramm, and his company, RotorWay Aircraft, Inc.
He’s been something of a voice crying in the wilderness about Rotorway Helicopters for quite a few years, and has been a steady fixture on the homebuilt rotorcraft scene — but it’s only in the last ten years or so that he’s really been able to offer the product he has wanted all along.
That product is the Exec, and by now it’s matured to a helicopter that, while a homebuilt, can’t be dismissed as such: It’s quite worthy of head-to-head comparison with production piston helicopters, even if B.J. and RotorWay don’t consider themselves to be competing in that market segment.
B. J. Schramm himself is an experienced rotorcraft engineer, and his first designs date back over 20 years. The first one offered to the public was the Javelin, a single-place ship with a steel-tube fuselage. In keeping with its era, it had a fiberglass pilot pod that looked like something right from the Jetsons TV show.
In those days, the hardest thing to find for a little helicopter was an engine with sufficient power-to-weight ratio, and B.J. embarked on a series of relationships with various liquid-cooled two-stroke engines derived from outboard motors. Like many young marriages, these were not without their occasional spats and even divorces.
At the same time, B.J., who’s nothing if not a savvy businessman, realized that it would be quite a while before he could live off the proceeds of his rotorcraft, so he founded (pardon the pun) another business: One of the most sophisticated foundries for non-ferrous metals in the country.
It’s obvious, though, that he did this at least partly with the fabrication of present and future helicopter parts in mind, since the name of the foundry is — what else? — RotorWay aka – Rotorway Helicopters.
As development of B.J.’s own helicopters continued, the RotorWay foundry kept busy turning out parts for such neighboring Ma and Pa businesses as Bell, Hughes, Sikorsky, and Motorola as well as an ever-increasing number of parts for B.J.’s own designs.
By this time, the Rotorway Helicopters Javelin had been retired in favor of the Scorpion, so-called because of the upswept stinger of its steel-tube tail boom; this, in turn, was soon joined by the two-place Scorpion II.
With the II, Rotorway Helicopters had its first product with real mass appeal — think of all those homebuilders’ wives who’d been saying don’t build anything you can’t take me along in.
With the greater size and weight of the two-place, Rotorway Helicopters had finally come up against the limitations of ex-outboard two-strokes, and the series of stormy marriages came to an end.
B.J. had finally had enough of compromises, and also had the not inconsiderable industrial resources of RotorWay foundries behind him, so the solution appeared simple: If you can’t find a suitable engine, build the (expletive, deleted) yourself!
Thus, the genesis of what was then the RW 133 engine, a 133-hp water-cooled four-cylinder opposed four-stroke. Do you grasp the magnitude of this undertaking?
People like Joe Horvath, Rex Taylor, or Peter Limbach will tell you how hard it is just to convert an already-engineered VW engine for aircraft use; RotorWay’s engine starts out as a few rough forgings for crankshafts, cams, and rods, and a stack of aluminum ingots that’ll be melted down to cast crankcases, cylinders, cylinder heads, manifolds, and so forth.
In subsequent years the engine increased in power and evolved into the present RW 152, and about the only major parts of it not made from scratch by Rotorway are the electronic ignition (Mallory) and the two-barrel carburetor (Dell’Orto).
By the beginning of the 1980s, B.J. realized that the homebuilding public was becoming extremely sophisticated, and wanted a product with more sex appeal than the somewhat angular Scorpion II, so he redesigned it to become the Exec.
The rugged steel-tube main structure, tying together the cockpit, landing gear, engine, “transmission” — of which more later — and main rotor system remained, but was now covered with a sleek fiberglass shell.
The former Rotorway Helicopters steel-tube tailboom, with its exposed V-belt tail rotor drive, was replaced by a monocoque aluminum structure (although the light, reliable, and inexpensive V-belt drive lives on inside it).
Finally, and most recently, the rotor system was re-engineered with asymmetric blades, unique in light piston helicopters and offering a major boost in performance, mounted in a new elastomeric-bearing rotor hub system.
Overall, the Rotorway Helicopters Exec looks remarkably similar to the turbine-powered Aerospatiale Gazelle, arguably one of the most handsome helicopters ever built.
With a high degree of control over both component price and quality due to in-house fabrication of almost everything larger than off-the-shelf fasteners, B.J. Schramm and his minions strove for an equal degree of control over both kit construction and homebuilder/pilot qualification.
Thus, when you buy an Exec kit (for a total investment, including tools and training, of about $40,000), you get quite a bit more than just the pieces to build a helicopter.
The plans are extremely complete and well done, and include exploded views, three-view drawings, and a series of over 500 see-do photographs — a sort of helicopter builders’ comix and stories — to take you through the process step-by-step.
Recent FAA decisions have allowed RotorWay to complete more of the process than they could in the past; for example, while the steel-tube airframe was always jigged, aligned, and tack-welded by RotorWay, all structural joints now come completely welded, with only minor brackets and tabs requiring field welding either by the homebuilder or by a hired gun.
There’s also much less welding required overall, since the former welded tube tailboom has been replaced by a monocoque structure of aluminum casting(!) bulkhead rings, stringers, and skins.
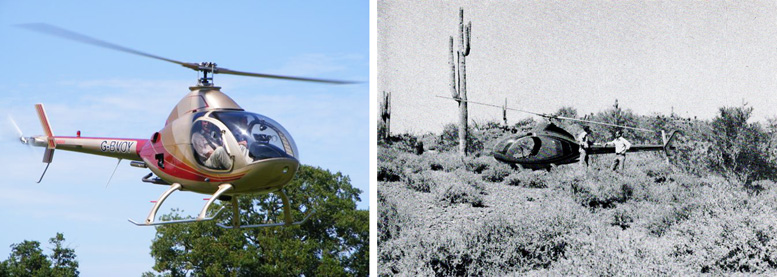
Since the Exec is fairly light, weight and balance are easy to determine.
It may seem a bit of overkill to use castings for bulkheads — but you begin to understand B.J.’s methods when you realize that these castings pick up the hangar bearings for the pulleys of the tail rotor drive. Part of the package includes extensive builder and pilot training.
Once you’ve completed your helicopter, but before you even run the engine, you come to RotorWays’ Sky Center near Phoenix, Arizona for Phase I training. There, you’ll spend a week in the classroom, learning not only basic helicopter aerodynamics but also how to balance and fine-tune your own ship.
This is considered an area that strikes fear into the hearts of even experienced pilots and mechanics, and most production helicopters are balanced using very sophisticated electronic equipment; according to RotorWays’ Stretch Wolters, an Exec properly balanced by a homebuilder won’t even register high enough on the scale of typical Chadwick balancers for further adjustment.
Rotorway Helicopters Phase I trainees also receive several hours of flight instruction in one of the Sky Center’s fleet of Execs.
This not only ensures that they’ll leave with sufficient skills to make safe liftoffs, hovers, and maneuvers in ground effect in their own Execs; it also keeps the factory’s Execs flying enough to make them the senior With Phase I under their belts, the new operators disperse to their homes for plenty of hover practice.
When they’re competent to perform a number of maneuvers and skill exercises, they return to the Sky Center and, after an initial screening, progress to Phase II — the full spectrum of helicopter flight.
After satisfactory completion of Phase II with any of several RotorWay instructors, they fall once again into the clutches of Stretch Wolters, who in addition to his other qualifications (including thousands of hours in RotorWay helicopters) is an FAA designated examiner.
Thus, you can essentially walk in off the street with no experience whatsoever, and emerge at the end of the process with not only a helicopter, but a Private Pilot/Rotorcraft license to exercise in it! I worked with Stretch during a recent visit to the Sky Center, currently located in Chandler but slated to move to the Glendale, Arizona, airport in the near future.
The original location, once well away from town, has been encroached on by other development such that the foundry and manufacturing facility have already been moved away; due to new buildings and obstructions, the Sky Center will soon follow, unfortunately forsaking a large building with hangar, shops, and lounge and four spacious helipads.
I spent the first hour or so in one of the facility’s video rooms sampling the tapes which are provided to homebuilders.
Complex subjects like rotor system balancing are very well handled, and given the relatively light weight of the helicopter (1320 lbs gross) weight and balance is determined by the relatively simple expedient of hoisting the whole thing by its rotor mast and moving weight around until it hangs at the correct angle.
We moved on to a classroom for a look at some of the ship’s components. Rotorway ensures correct assembly by shipping critical parts groups as complete subassemblies; thus, for example, the main rotor shaft comes to the homebuilder with the entire cyclic and collective control system (a group of RotorWay aluminum castings, of course) as well as the rotor hub already assembled and in place.
Similarly, the secondary drive unit, a multi-belt aluminum sheave with the vital overrunning clutch in its center, comes pre-assembled and tested.
The engine, of course, is shipped ready to run — in fact, it’s already run several hours on a dynamometer to ensure that it meets specifications. Earlier, I put the word transmission in quotes; this is because the Exec doesn’t have the usual helicopter assemblage of gears and pinions.
Instead, primary drive from the engine is a group of V-belts to a large sheave containing the clutch, while secondary drive from the sheave is a sprocket with large roller chains driving a similar, but larger, sprocket at the base of the main rotor shaft.
The chains run in an oil bath, and the tail rotor V-belt takes off from the secondary drive. The system has no torque limitations, and belt slippage (allowed by a loose idler that’s locked into position after engine start) takes care of torsional peaks during startup.
We went out to the helipad and Stretch walked me through a careful preflight. With just about everything on the ship accessible from ground level, it’s easy to check it over very thoroughly.
One item that’s critical is battery location for correct C/G; when the ship is flown solo, the battery goes under the cockpit floor, and when flown dual it goes into the tailboom, with cables provided at both positions.
There’s a good deal of room in the cockpit once you’re aboard, but getting in requires a little technique as you duck in through the door. The best method seems to be to thread your inboard leg in past the cyclic, duck in, then haul the outboard one in after you.
I managed with no more effort than your typical bogged hippo getting out of a mudhole; Stretch, who lives up to his name at well over six feet, slid gracefully into the right seat before I could even see how it was done.
The standard instrument panel, including RotorWay’s trademark separate engine and rotor tachometers, goes ahead of the left rudder pedals, but many builders opt for the more conventional center instrument pedestal as on our demo ship.
Startup is a matter of flipping a few switches, verifying that the primary drive idler T-handle is pulled out, and hitting the button on top of either cyclic; the engine lit at once, and the blades began to turn immediately.
As soon as they come up to speed, the T-handle is pushed in to lock up the primary drive. Unlike most other helicopters, the Exec is started with the collective about a third of the way up; in fact, the only time it’s lowered past that point is during autorotations.
With the ship warmed up, Stretch coached me through the standard liftoff procedure for neophyte Exec pilots: Hold a little pedal, ease the cyclic until pressures are balanced, and come up slowly on the collective until the helicopter gets light on its skids and tries to turn.
Set the pedals to stop the turn and continue up with the collective until liftoff. A slight cyclic correction is necessary as the helicopter lifts into a hover, but I found it quite stable and easy to control.
There’s no question that it’s a small, light helicopter that responds immediately to changes in control pressures, but it was not nearly as twitchy as I might have thought given its small size, and control pressures are actually quite firm.
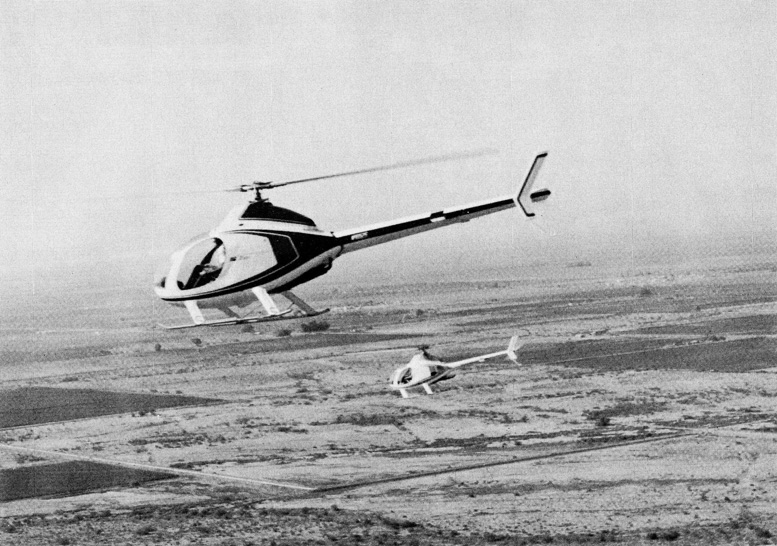
When you buy an Exec, you get an excellent package of builder and pilot training courses.
The elastomeric rotor bearings minimize feedback of one per rev forces through the controls, and throttle-collective correlation required only a minimum of throttle twisting.
Stretch made the first departure, since the new construction around the old Sky Center requires dodging among ranks of parked truck trailers, and we found some more open space to let me feel out the ship. It’s quite stable in cruise, and there’s some pitch-roll coupling requiring forward or back pressure to maintain altitude depending on the direction of turn.
The aerodynamics of the fuselage and rotor system interact such that lowering the collective tends to pitch the nose up, and raising it pulls it down, so the usual coordination exercise of accelerating and decelerating becomes somewhat superfluous.
Making a quick stop requires little more than reducing collective, keeping the nose straight with pedal, and letting pitch attitude pretty much take care of itself.
As a result of this, RotorWay’s height velocity diagram goes clear down to the ground anywhere past about 65 mph; an engine failure at that speed still leaves the pilot plenty of energy to slow up, flare, and set down.
Autorotation performance has really been improved by the asymmetric blade airfoil, so much that Stretch advocates controlling the touchdown point primarily by adjusting collective (and hence rotor speed) rather than airspeed.
With about 65 mph established in the descent, raising collective to pull the turns down to the bottom of the green reduces rate of descent to about 1300 fpm, while still allowing for a flare at the bottom to bring the speed back up.
Keeping the rotor speed at the top of the green runs the rate of descent up to about 1800 fpm. At low level, we also sampled yaw control with no pedal inputs, as would be the case in a tail rotor failure.
The ship could be slowed to not much over 20 mph and still pointed straight ahead; at that point in a real failure you’d roll off the throttle, ease back, and set down at about five mph pointed straight forward.
We returned to the Sky Center and Stretch talked me through the standard Exec approach — rather low and fast compared to other helicopters, but ending in a hover over the pad with a minimum of power change.
A minute or two of cool-down, and we shut down — following which Stretch instantly restarted the engine for a moment just to show me how readily it cranks up, hot or cold. Overall, I was quite impressed. The Exec weighs about as much, empty and loaded, as the Robinson R22, and it’s about as fast.
Altitude performance isn’t quite as good due to the higher disk loading — but let’s face it, light reciprocal helicopters aren’t ideal for hot-and-high operations in any case, and neither RotorWay nor Robinson suggest that they are. (Even so, I know of at least one RotorWay operated regularly above 6000 feet in Colorado, and Execs have flown well over 10,000.)
Is the Rotorway Helicopters Exec the only relatively low-cost way to own and operate your own helicopter? Not quite: For a similar initial investment you might find an elderly Hughes, Brantly, or Hiller more or less ready to fly.
Bear in mind, however, that these are all certificated helicopters full of life-limited parts that are very expensive at best and impossible to find at worst — and, since they’re certificated birds, you’ll have to have them worked on by certificated mechanics.
Yes, you can get into the air for less money, and right away — but it’ll catch up with you very quickly! RotorWay makes no effort to compete against certificated helicopters, new or used, for those operators who need to operate one; it’s an apples vs. oranges comparison.
If your helicopter needs are primarily for personal transportation or recreation, though, the Exec has a great deal to offer, not least of which is the fact that by the time you’re licensed in it you’ll have an extremely thorough grounding in helicopter theory, construction, and maintenance.
Besides, it must be quite a thrill to arrive somewhere in a spiffy helicopter and be able to say, when asked what kind it is, “I built it myself!”
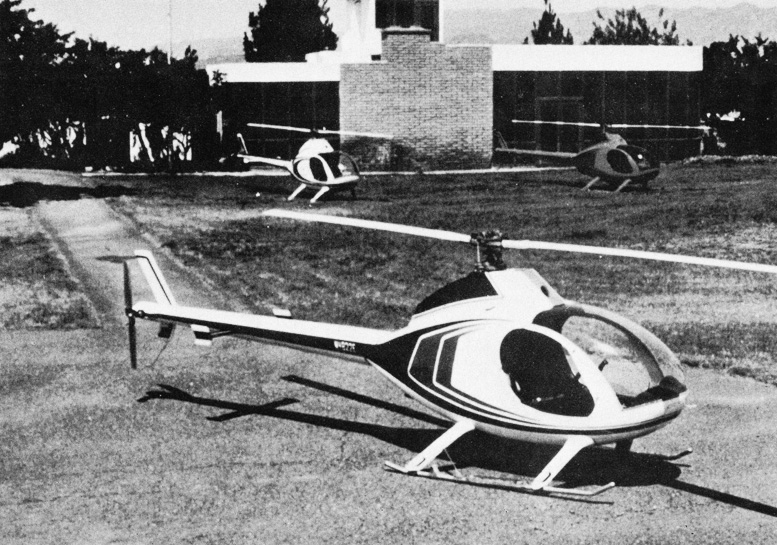
Autorotation performance has really been improved by the asymmetric blade airfoil.
ROTORWAY EXEC PERFORMANCE SPECIFICATIONS |
|
---|---|
Power Plant | RW-152 Water-Cooled Four-Stroke 152 hp |
Seats | 2 |
Gross Weight | 1320 lbs |
Empty Weight | 830 lbs |
Equipped Useful Load | 490 lbs |
Pilot & Passenger Seat Load | 380 lbs |
Fuel Capacity | 17 gal./110 lbs., 5 gal./aux. |
Rate of Climb | 1200 fpm |
Hover In-Ground Effect | Single-Place 10,000 ft Two-Place 7,500 ft |
Hover Out-of-Ground Effect | Single-Place 6,800 ft Two-Place 4,500 ft |
Service Ceiling | 12,000 ft |
Range Max. Fuel, Optimum Cruise Power | (one person & 5 gal. aux.) 275 mi/2.75 hrs |
Range Max. Fuel, Optimum Cruise Power | (two persons) 201 mi/2.1 hrs |
Normal Cruise | 95 mph |
Max Airspeed @ Sea Level, Standard Day | 115 mph |
1989 EXEC GROUP DOMESTIC PRICE LIST
GROUP I-A – $3850
-
B-Tool Kit
-
Tail Boom Group
-
C-Airframe
-
Landing Gear
-
Airframe Brackets
GROUP II-A – $4575
-
B-Cabin
-
Floor Pan
-
Seats W/Black Vinyl
-
C-Doors
-
Windscreen
GROUP III-A – $4016
-
B-Cyclic Control
-
Collective Control
-
Directional Control
-
Engine Mount
-
Water Pump
-
Alternator
-
Pilot/Passenger Seat Belts
-
W/Shoulder Harness
-
C-Tail Rotor
-
Tail Rotor Drive
GROUP IV-A – $6116
-
B-Main Shaft Assembly
-
Elastomeric Rotor Hub
-
C-Secondary Drive
-
Oil Bath
GROUP V-A – $4587
-
B-Fuel System
-
Clutch Torque Link
-
Instrument Panel/Wiring Harness
-
Engine Instruments
-
Rotor Tachometer
-
C-Oil Cooling System
-
Radiator
-
Fan Shroud
-
Fan Drive
-
Stand Pipe & Hoses
GROUP VI-A – $4780
-
B-Asymmetrical Rotor Blades
-
C-Elastomeric Bearings and Thrust System
GROUP VII-A – $7776
-
B-Standard Exhaust System
-
Heat Shielding
-
Battery
-
C-RW 152/D Engine
TOTAL: $35,700
OPTIONAL EQUIPMENT
-
Airframe Special: $2500
-
Dual Controls: $231
-
Skid Pants: $215
-
Ground Wheels: $145
-
Air Plenum: $80
-
Carb. Temperature Gauge: $80
-
Stainless Steel Exhaust: $295 or $468 if sold separately
-
Luggage Compartment: $125
-
Pioneer Photo Tach: $325
-
Instrument Pod: $250 or $500 if sold separately
-
Hi-Temp Cooling Fan: $250
CRATING CHARGES
-
GROUP I-A: $95
-
GROUP II-A: $125
-
GROUP III-A: $60
-
GROUP IV-A: $105
-
GROUP V-A: $70
-
GROUP VI-A: $75
-
GROUP VII: $95-A
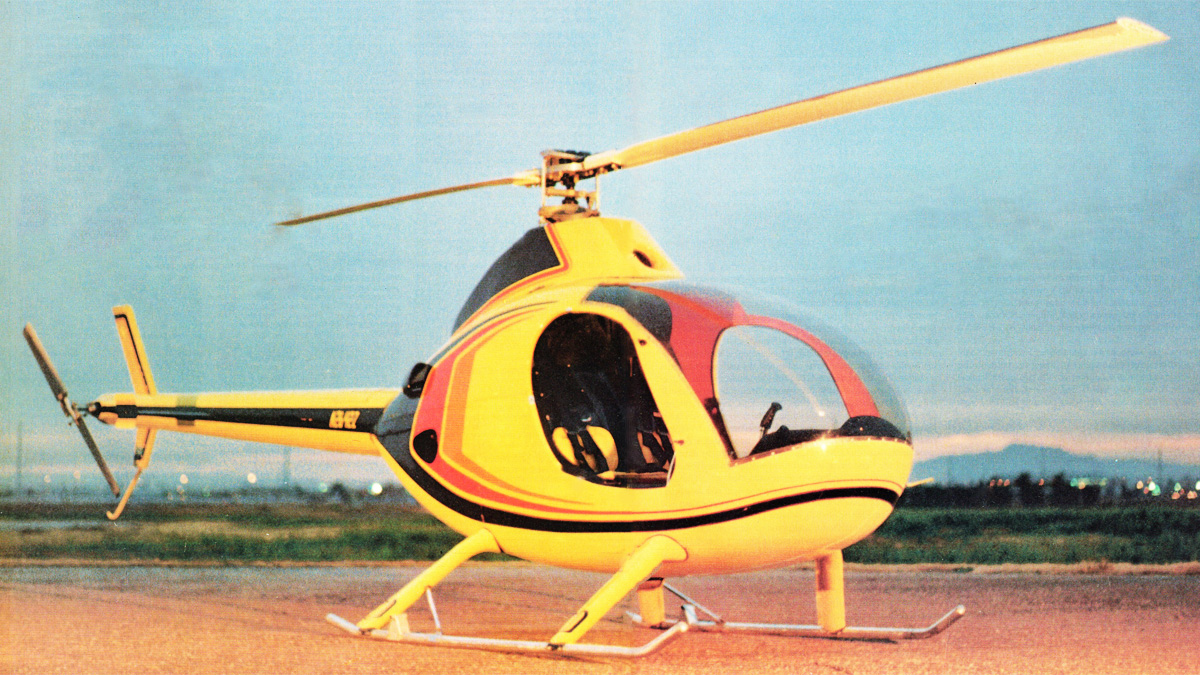
Be the first to comment on "Rotorway Helicopters Executive Decision"