UltraSport 496 and 254 Kit Helicopters
A technical marvel – American Sportscopter UltarSport 496 – A recreational revolution
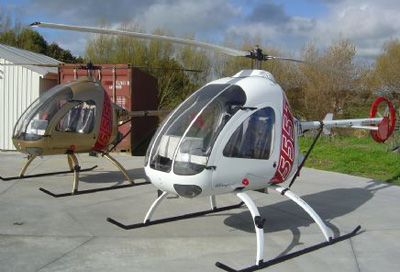
Aftermarket turbine powered Ultrasport two seat helicopter.
The sport aviation historic landscape is littered with the refuse of countless shattered dreams. In the sport rotorcraft arena, it is littered with more such tragedies than any other segment of aviation, an important consideration for UltraSport helicopters designers.
The reason for this is twofold, as the sport aircraft community tends to attract its share of offbeat personalities with delusions of grandeur, and of course the technical requirements of designing and manufacturing a proper rotorcraft are greater than for any other type of flying machine.
Worse, in the sport rotorcraft community, sport helicopters are a far more demanding discipline than gyroplanes or autogyros. It may be a minor miracle that any proper sport helicopters have ever seen the light of day. They are simply too difficult to design, too hard to manufacture, and require more pilot competence from their builders than any equivalent fixed wing aircraft.
Unfortunately, that lesson has not been learned by a number of sport helicopter designers. Some of the tragedies of the past few years are moot testimony to that fact. In the two-place sport helicopter community only three aircraft appear to have achieved the requisite combination of technical expertise, engineering/manufacturing competency, and market acceptance.
Of these, one company has distinguished itself in regards to the first two parameters but is struggling with the third. I speak of American Sportscopter Inc., a firm with more rotorcraft “smarts”, possibly, than all other such companies combined. A civilian and military contractor and engineering think-tank, the parent company to American Sportscopter Inc. has an extraordinary background and extensive Helicopter engineering talent and capabilities.
These folks have smarts up the proverbial wazoo… but unfortunately still have a way to go in communicating how extraordinary their machines are to the general public. But then again, it is not surprising to me, from my experience in that industry, that the folks with the most to brag bout often don’t do that good a job of bragging.
As I said, the engineering capabilities of this company comes second to none in the sport rotorcraft field. As a result, it was no surprise to me several years ago while testing their single-place Ultrasport 331 (a slightly heavier version of their Ultralight “254”, with a few more goodies and options) that I found that they had not only designed an easy-to-fly sport helicopter, but they had done it ruggedly and capably.

Ultrasport helicopter tailboom.
The little 331 turned out to be a hell of a flyer, and after watching the demo pilot gleefully and purposefully slam the tail boom into the ground during several quick-stop manoeuvres, it was obvious that this was one strong little puppy. It remains one of the few single-place sport helicopters that we can currently recommend to the flying public. Most impressive to me, as I toured the factory, were the manufacturing fixtures and testing gear that filled the area.
Unlike most other rotorcraft manufacturers, the Ultrasport kit helicopter had seen the benefit of extensive structural and fatigue testing. Critical items like the rotor blades were placed in bending fixtures and run through millions of cycles.
Computer analysis of critical structures defined potential weak areas and allowed for a more rugged structure. In other words, these folks did their homework and they did it well… which is what you expect of a company that builds prototype components for the US Military, various defense contractors and some of the most picky mission-critical companies and projects in the world.
Folks, these people are no fools; they are not stupid. They have some of the best minds in the business and with all of the money that civilian and defense contracting pays, you know they have to be in the sport helicopter business for the sheet love of it, because it sure doesn’t pay that well.
So…it was with great anticipation that I travelled up to Newport News, VA to be the first to sample the capabilities of the Ultrasport 496 two=seat sport helicopter. The machine was still in flight-testing, but had logged enough hours that Ultrasport helicopter was deliberately looking for input on the handling and capabilities of their aircraft, and were smart enough to seek same. Despite rain, drizzle, and wind, I drove up to the little yellow and green bumblebee expecting a positive experience, and enjoying the fact that I was not to be disappointed.
Looking Through the Innards of UltraSport Helicopters
Before we get to play, let’s explore a little history and examine the specs for the Ultrasport 496 helicopter, a two stroke 115-hp, two-seat, side-by-side, sport helicopter with a two-bladed semi-rigid rotor system, and a conventional tail rotor system.
The Ultrasport 496 kit helicopter stands 7.8′ tall and is 19.8′ long. The rotor blades span 23′ and the tail rotor is 2.6′. This helicopter uses a Hirth F30 engine, which gives it a top speed of 104 mph and a cruise of 69mph. Rate of climb is 1000 fpm and it has a service ceiling of 12,000′. Goss weight is 1130 lbs and it has an empty weight of 540 lbs. With a full load of fuel (16 gal), you get a payload of 445 lbs. Range on the helicopter is 150 miles. HIGE is 10,800′ and HOGE is 7000′.
‘Dem Helicopter Blades
Obviously, rotor blades are to a rotorcraft what wings are to an airplane…but few people have any concept of how difficult it is to engineer an aerodynamic surface that has to spin at several hundred rpm. Fixed-wing aircraft can experience a number of minor and secondary failures of ailments in a wing that isn’t being beat up too badly, but a rotor spinning at hundreds of mph and being pulled apart by many thousands of pounds of divergent force requires that the engineering be flawless.
The Ultrasport helicopters unlimited-life main rotor blade system has been exhaustively designed for durability and efficiency. The blades, laid up by hand and cured in 260-degree ovens, possess eight degrees of twist linearly and have tungsten leading-edge weights in the outside 50% of the blades. All composite, the moderately cambered blades featured a graphite/epoxy/fibreglass spar pre-moulded and bonded to a Nomex honeycomb trailing edge core structure, which is wrapped in a fiberglass skin, and then heat cured.
A polyethylene erosions trip is applied to the leading edge after primary finishing to enhance the long-term integrity of the rotor. The two-blade main rotor hub is a semi-rigid, underslung, teetering type system of all aluminium construction.
The TT (Tension/Torsion) strap has been designed for an infinite life at 120% of rated stress loads and has been tested to failure at 26,500 lbs.
A rubber shaft bumper allows for moderately high-wind start-ups without hazard of damage. The main rotor’s cyclic control is supplied via an overhead cyclic (though a floor-mounted T-bar cyclic control is available as an option).
The overhead cyclic stick actually couples directly to the swash plate with a small, adjustable walking beam in place to reverse control input so that forward stick produces forward cyclic (otherwise, it would really get confusing!).
The walking beam may be adjusted to produce control response ratios to suit pilot preference and experience. The helicopters efficiency of the system is such that the rotor produces 14 lbs of lift for each horsepower’s input due to the low disk loading.
The tail rotors are built similarly to the mains…except that the tail rotor trailing edge uses a core of Rohacell foam. The airfoil and rotor tips have been specifically designed to minimize external noise (tail rotors, due to their high tip speeds, are a major cause of helicopter noise). The ring-shaped fan guard originally started life as a fenestron (something of a ducted fan) but flight-testing proved that to have unsuitable flying properties.

The American Sportcopter Ultrasport 496 kit helicopter at Avalon Airshow – Australia
A more conventional tail rotor has been substituted, though the vertical fin has retained the ring configuration to serve as both a stabilizer as well as a protection system for the tail rotor – something it does very well. The tail boom is a metal construct and the later versions of this assembly have been mounted higher in relation to the fuselage in order to add some ground clearance.
The tail rotor is driven by the main rotor transmission through a 1″ aluminium drive shaft supported by four hangar bearings inside the length of the tail boom. The tail rotor is driven at 75% of the engines’ speed to a 90-degree gearbox mounted on the end of the tail boom. Its gearbox is grease lubricated and cooled by external airflow, still allowing for a normal maximum operating temperature of 125 degrees F.
American Sportscopter Ultrasport Helicopters Airframe

The American Sportcopter Ultrasport 496 composite helicopter cabin.
The structural core of the 496 helicopter is the pilot seat assembly, which serves as support for both the fuselage bulkhead and the firewall.
The seat assembly itself serves as the base torque box to which everything is subsequently attached. It is composed of a lightweight, but extremely strong, matrix of graphite, epoxy, and Nomex honeycomb cores.
Both helicopters actual engine mount/assembly is literally bolted to the rear of the seat. The fuselage fairing is non-structural and is a graphite/epoxy construct proven to be both light and durable.
The UltraSports windshield is free-formed in order to offer maximum visual clarity. The UltraSport helicopters landing gear bows are sandwiched out of aluminium and glass/epoxy plies offering strength as well as flexibility.
Landing skids have so much flexibility that they can deflect until the fuselage hits the ground without permanent damage. This assembly has been designed to allow for 2.5G. impacts without structural failure. The UltraSport helicopters landing skids themselves are aluminium.
The interior cabin is 53″ long and 48″ wide, sufficient for those of us who don’t get to the gym as often as they should and you know who you are), and the cabin is 59″ tall with a surprising amount of headroom – even after one sits up straight, ensconced in a headset.
An instrument pylon is centred in front of the cabin, and boasts sufficient room for radios, instruments, and needed indicators. It is easily accessible with slight reach from either side of the UltraSport helicopters cockpit, and its visibility is unrestricted by anything in the cabin (especially with the floor-mounted cyclic).
American Sportscopter Ultrasport Helicopters Control System
The Ultrasport 496 helicopter uses a two-bladed, underslung, teetering-type rotor hub. The main body of the hub is computer machined from 2024-T4 aluminium billet. The blades are retained to the hub against centrifugal force with a “tension/torsion” pack. This assembly requires no lubrication, has an infinite fatigue life and is fail-safe.
The one-piece hub is designed to insure a high natural frequency of the hub and blades when rotating, in order to reduce airframe fatigue that occurs with multi-piece two-bladed hubs. The entire assembly has been structurally tested to conform to FAR Part 27 certification standards.
The Ultrasport 496 kit helicopter normally features an overhead-mounted cyclic control assembly. My flights in the 331, (the single-place the variant) showed that this was an agile and adaptable means of controlling the aircraft. The Ultrasport 496 production aircraft that we flew, however, featured the new, optional floor-mounted cyclic – very similar to the control assembly one finds on the Robinson R-22 and the R-44 helicopters.

The all composite Ultrasport 331 kit helicopter
On the UltraSport helicopters, access to the left-side mounted collective control system is fairly unencumbered and this floor-mounted cyclic system is well positioned in the cockpit as far as its mounting goes (but I would personally prefer that it be taller by an inch or two in order to give each pilots’ legs a little bit more clearance between them and the end of the cyclic assembly). Mechanical throws and pressures reveal minimal friction, and there is little “slop” in either system…though in-flight adjustable collective and throttle friction adjustments are standard equipment on the 496. The tail rotor is controlled by conventional anti torque pedals and equipped with a quick-disconnect cable installation. Pedal position was conveniently placed, easily accessible, and required only light pressure to motivate.
American Sportscopter Ultrasport Powerplant
The Hirth F30 is a four-cylinder, two stroke powerplant designed to produce 120 hp (115 hp in the Ultrasport) using four Mikuni carburettors. The carburettors are pressure altitude compensating. The Hirth series of two-strokes was selected for use in the Ultrasport Helicopter series because of their high power to weight ratio and a surprisingly flat torque curve that sure makes both mechanical and pilot induced collective/throttle correlation a far easier chose than it might be with another engine.
EDITORS NOTE: You’d be hard pressed to find an Ultrasport with its original two stroke engine nowadays. While a couple have found four stroke power, turbines are all the rage for re-powering the Ultrasport range of helicopters.
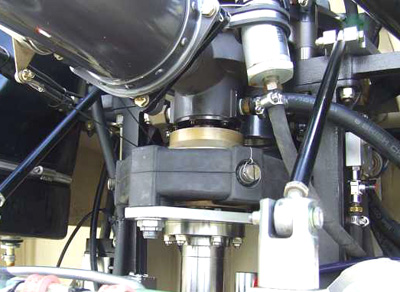
The engine drive isolation rubber coupling to the main gearbox.
The F30 offers a 35% power reserve at sea level, standard day conditions. Hirth offers a 1000-hour TBO and a one-year factory warranty on their engines. The 135-lb engine features dual CDI ignition. Al-Nikasil coated cylinders, and dual fan cooling. The Al-Nikasil cylinders are particularly notable in that most engines on the market are built with steel sleeved cylinders. Steel sleeves are cheaper than Nikasil, but steel cannot dissipate heat as efficiently as aluminium and expands at a slower rate. As the heat in a steel sleeve cylinder engine increases, the piston expands faster than the cylinder wall, steadily decreasing the piston clearance (and thereby setting up prime conditions for an engine seizure and a sudden letdown).
To compensate for this, engines utilizing steel sleeve cylinders, must run lower CHT and EGT temperatures. Hirths’ cylinders are of aluminium alloy and have NO sleeves. The cylinder walls have been treated with the aforementioned Nikasil process (which is not a coating, by the way, as the process alters the molecular structure of the aluminium allow to produce a hardened surface that cannot peel and is more wear resistant than steel sleeves).
Because the cylinders are still an aluminium alloy, their expansion properties as well as their thermal conductivity are virtually unchanged. This design allows heat to be dissipated quickly and efficiently. The piston is also made from an aluminium alloy. The piston alloy is slightly different and expands slightly less then the Nikasil cylinder. This combination of cylinder treatment and matched cylinder and piston materials creates an extremely size resistant environment. This is also why Hirth’s engine design can handle cylinder head temperatures of as much as 600 degrees F without failure.
Although the Nikasil process is more expensive, the resulting increase in the engine’s lifespan, performance, and reliability more than offsets the cost (and may keep you in the air, instead of forcing you down).
The UltraSport Helicopters Transmission
The power/drive system consists of a two-stage helical spur gear gearbox with a 4.18:1 ratio, rated for 120 hp continuous. Since there is a 2.64:1 reduction ratio in the engine gearbox, the overall reduction ratio is 11:1. The transmission is equipped with both chip and thermal detectors to guard against unforeseen failure.
An external cooler, sump and pump circulate pressurized oil throughout the gearbox. Actual power is derived through a one-way centrifugal and Sprague clutch system. The clutch offers sufficient slippage to allow for a good engine to rotor power transition and smooth rotor speed up. Start up is made easier due to the fact that the centrifugal clutch does not engage the main rotor until the engine sees 2000 rpm.
All transmission components in the UltraSport helicopters have been manufactured to aerospace specifications by the same company that make hubs and gearboxes for Bell and Eurocopter helicopters. These are no drive belts or chains in the transmission chain.
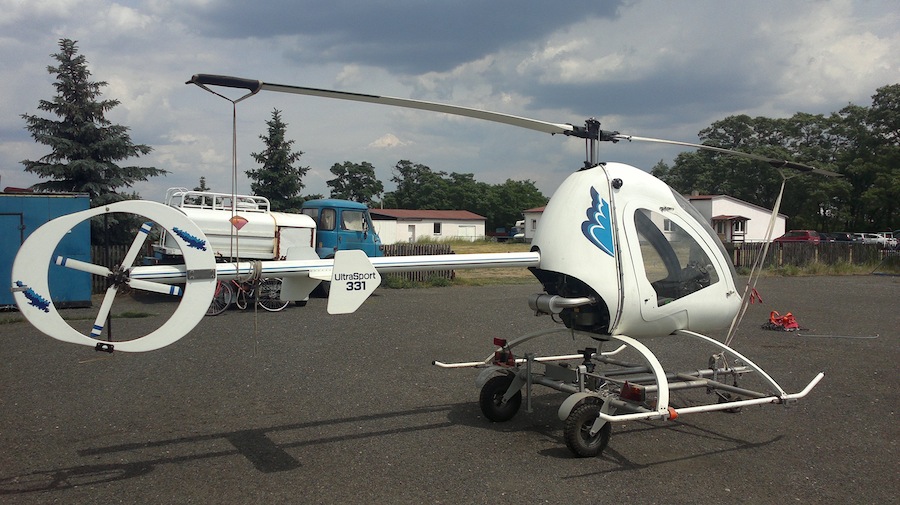
American SportCopter UltraSport 331 helicopter
UltraSport Helicopters Testing and Development
Okay… I know it sounds like I’m flogging this particular horse to a lather, but I cannot emphasize how lavishly engineered and tested this helicopter has been. Long before it flew, this machine was lofted and examined on computer-based programs that were specifically designed for utilization in aerospace development. When the original Ultrasport prototype was built, the aircraft’s rotor blades, pitch links, control system and rotor shaft were instrumented with strain gauges.
A 20-channel data recording system was installed, and five accelerometers were attached to the airframe of the test vehicle. During flight test, not only was an experienced test pilot used, but also the instruments involved in the testing presented an extraordinary pool of information from which American Sportscopter could extrapolate potential problem areas and engineer against them. I know of no other company that has done anything even remotely near this.

The world first all composite kit helicopter.
The aircraft was involved in an extensive series of fatigue tests, and a number of parts were tested to absolute destruction. Further, a version of the 496 is currently flying as a military drone in a US Defense Program, and I guarantee you that this remotely piloted version received far more abuse than any test pilot would be willing to subject him or herself to.
Last year, a team led by Science Applications Int’l Corporation was awarded a contract by the US Navy for its Vigilante vertical take-off and land (VTOL) unmanned air vehicle (UAV) based on the Ultrasport helicopter kit.
For its military role, the Vigilante can be transported on and deployed from frigates and other Navy ships that are likely to reach the battle-space before aircraft carriers. As a result, the Vigilante will be able to supplement the mission of the Navy’s jet fighters by providing early reconnaissance and payload capabilities quickly and cheaply.
VIDEO: Ultra Sport 496 Turbine Helicopter
As modified for the Navy’s use, the Vigilante will carry enough fuel to allow it to operate for up to 16 hours. Its imagery payload has an infrared imaging sensor and a daylight colour television camera. A great toy,eh?
The UltraSport Helicopter Kit
The $49,000 Ultrasport 496 kit features full dual controls, doors, and engine instruments. All parts and components are either aviation or military spec, and no automotive or non-aviation components are used in this kit. The builder is required to supply tools and paint, airspeed/altitude/compass and other associated instrumentation, as well as any radios or transponders they wish to install, and a batter for the electric starter. Upholstery, seat cushions, and lights are builder supplied.
Optional floats are available for $2300 and a BRS emergency parachute system, which fires off the top of the rotor mast, is in development. The only kit available for the Ultrasport 496 is the “quick-build” version and the factory quote 80-100 hours of assembly time (using basic tools). If you get fancy with options, of course, that might take a little bit longer… but it’s pretty obvious that a 496 is a fairly quick-building beast.
As modified for the Navy’s use, the Vigilante will carry enough fuel to allow it to operate for up to 16 hours. Its imagery payload has an infrared imaging sensor and a daylight colour television camera. A great toy, eh?
Inspecting the Ultrasport 496 construction manual is a joy. Well illustrated, the 1″ thick manual allows for a methodical, easily understood construction process that not only does a great job of describing and documenting the assembly of the Ultrasport 496, but includes a generous series of appendices to further help a neophyte understand their aircraft, its components, its hardware, and the intricacies of sport helicopters. Builders of the single-place machine have given me very positive comments about the manual and about the level of support they experienced form the company.
VIDEO: Ultra Sport 496 on flight to nowhere
Factory training and orientation is available, and American Sportscopter has taken to hosting demo sessions in the factory two-place at a nearby airport with increasing regularity. The factory has a policy that kits will be shipped without main rotors until a purchaser can demonstrate some kind of helicopter proficiency.
Such evidence of proficiency includes a sole endorsement signed by a Helicopter CFE, and actual license, or other significant evidence of professional training in a Helicopter. We applaud them for the tactic.
UltraSport Levitation!
The day I came up to test fly the UltraSport helicopter was not exactly what one would call a best-case scenario; as a matter-of-fact, it was a pretty dreary, occasionally rainy day. Add to that winds varying from a few knots to nearly 20 knots, and you have the kind of day that can tax a small helicopter to the utmost.
The Ultrasport 496 is a cute little rascal. Since it sits fairly low to ground, one needs to bend down slightly and back one’s self into either side’s seat to swing in their legs behind them. Once inside, I found cabin room to be plentiful and noted few discernible restrictions in the cockpit.
There was ample door room to swing my feet in without having to draw them in too closely and I was pleased to find adequate hip room in the aircraft – even with a real, live adult next to me. Like most helicopters, the collective pitch/throttle control system sits on the left side of the seat. The optional T-bar cyclic is positioned well forward too the floor but could be just an inch or so taller for my tastes. A quick check of control continuity on the ground revealed light-to-moderate mechanical forces, and no evidence of binding or slop.
Despite the cool temperatures and the light rain, we elected to fly the 496 with the doors off, in order to enjoy every sensation this aircraft produced. One thing was evident as I and the factory demo pilot seated ourselves… those skids are very flexible, and settled perceptibly as we added our weight to the aircraft.
The Hirth F30 started up rather quickly, and idles very nicely just under 1500 rpm. At this speed, the rotors remain somewhat stationary but as you crank on some throttle and pick up to 2000-3000 rpm, the clutch takes hold smoothly and the rotor spins up readily. There is a bit of stick-shake that occurs as the rotors start spinning up, but it damps out quickly once the rotor gets close to 100 RPM.
Model | 331 Single Seat | 496 Two Seat |
---|---|---|
Engine Option 1 | 65 hp Hirth H32 electric start, dual carb | 105 Hirth H30ES electric start fuel and oil injection |
Engine Option 2 | Aftermarket turbine | Aftermarket turbine |
Transmission | 12:1 Planetary | 12:1 Two stage |
Endurance | 38 lt tank – 3 1/2 hrs | 60 lt tank – 3 hrs |
Ceiling | 12,000 ft | 12,000 ft |
HOGE | 10,800 ft | 7,000 ft |
HIGE | 10,800 ft | 7,000 ft |
Rotor Blades | FAA Cert. Infinite Life Composite | FAA Cert. Infinite Life Composite |
Main Rotor Blades | 21 ft dia. 6 inch chord | 23 ft dia. 6 inch chord; |
Tail Rotor Blades | 2 ft 6 inch with 2 inch chord | 2 ft 6 inch with 2 inch chord |
Cabin Length | 52 inch – 1,320 mm | 53 inch – 1,346 mm |
Cabin Width | 30 inch – 760 mm | 48 inch – 1,220 mm |
Cabin Height | 59 inch – 1,500 mm | 59 inch – 1,500 mm |
Cruise | 65 mph – 105 kmph | 69 mph – 112 kmph |
Top Speed | 104 mph – 167 kmph | 104 mph – 167 kmph |
Empty Weight | 330 lbs – 150 kg | 395 lbs – 245 kg |
Useful Load | 320 lbs – 145 kg | 480 lbs – 268 kg |
Gross Weight | 650 lbs – 295 kg | 875 lbs – 514 kg |
Width | 8 ft – 2,438 mm | 8 ft – 2,438 mm |
Height | 7 ft 10 inch – 2,438mm | 7 ft 10 inch – 2,438mm |
Length | 19 ft 2 inch – 5,842 mm | 19ft 9 inch – 1,620 mm |
Pre-flight checks included testing the Sprague clutch in order to make sure that it would disengage itself in the event of an engine failure. This is done by revving the engine and rotor up to near flying speed, and twisting off the throttle suddenly to make sure that the rotor is still not coupled to the transmission (decelerating it drastically).
This check is often called “splitting the needles”, which describes what occurs as one idles the engine suddenly from a near full power run-up… whereby the rotor tach needle stays fairly close to where it was, and the engine tachometer needle drops precipitously.
The Hirth offers excellent throttle response…and an overt absence of any “power spikes”, meaning that there is a fairly linear response curve between the engine and the throttle. In any helicopter, especially one with modest mechanical or no correlation, this can be a very significant air. Start adding power, and one starts to rise aggressively for as much as 6-8″ without even leaving the ground! Those springy skids are pretty compressed when there are two people aboard so it takes a little bit of altitude to decompress the skids before one can even leave the ground.
Unlike the early prototypes of the single-seaters that I flew, the Ultrasport 496 has managed to dampen out a fair amount of airframe vibration and eliminate the soporific side effect that such vibes often had on ones backside.
Coming up to full power, and easing in positive collective, the Ultrasport 496 lifts off readily, and required minimal lateral cyclic to keep things steady. Picking up to a 3′ hover, I noted good control response with modest pressures, and a pleasant lack of sensitivity to the lightly gusting winds that were growing outside. That large tail guard/vertical fin does weathervane strongly, if uncorrected, but minor corrections to the antitorque pedals will point things the way you want them rather quickly.
Unlike the R-22 and Hughes 269, the Ultrasport’s hover behaviour resists any control sensitivity. Small cyclic movements are rewarded by small control responses and no discernible mechanical feedback. The degree of control linearity is impressive and contributes to the machine’s excellent manners. All but the most aggressive cyclic control pressures are generally pretty light. I found the T-bar cyclic to be easy to use, and fit the aircraft very well. Those that have flown Robinson helicopters know this configuration well, and will immediately find themselves right at home.
Anti-torque action is very good and the pedals produce agile response. Our first test flights were done in 4-8 knot winds, so good anti-torque response was necessary for agile crosswind and downwind hovering. Pedal pressures are light, and response is mostly linear until you get to high deflections.
In terms of collective control, I particularly appreciated the fact that the throttle control range was well within the range of a single normal twisting motion, and didn’t require one to have to loosen their grip and then add more throttle. Pressures are moderate, the physical range is generous, and collective response is excellent, with modest mechanical friction.
I spent about 10 minutes playing in the hover to feel out the 496. While I think Ultrasport’s claim of a 35% power reserve for the Hirth engine is a bit generous, there is no question that the Hirth has sufficient power to do the job…and then some. In no time at all, I started transitioning to some forward speed, and experienced a fairly quick translation to forward flight.
VIDEO: UltraSport 331 Kit Helicopter in Thailand
The Ultrasport’s speeds through “translation” with a minimum of buffeting and only a minor amount of “hunting” directionally. That big vertical fin really comes alive in forward flight, and eases cruising chores greatly. While the machine has a top speed in excess of 100 mph, the 496 seems most comfortable at about 75 mph. Pushing much past that takes an excessive amount of power, and though well behaved, it’s obvious that this is not a normal flight regime for this aircraft. Further, I noted a small amount of inward deflection on the windshield at airspeeds in excess of 80 mph.
Once established in cruise flight, only modest lateral cyclic input corrections are occasionally required, and the vibration level is not unpleasant. I understand that climb rates near to 1000 fpm are quoted for this aircraft but 500-700 fpm produces a good climb in the low to mid-50s, with good visibility and a surprisingly modest amount of power.
This baby has great in-flight visibility and bopping around the field in it was a very pleasant effort, as the large doorframes offered good peripheral visibility and that huge windshield was unrestricted until it met the doorframe. The two-place Ultrasport is a much heavier machine than its single-place cousins…but its rotor inertia is still impressive. On a few low-altitude downwind runs over the airport, I allowed the rotor rpm to dissipate to approximately 90%, and was able to recover it readily by loading up the rotor slightly with aft cyclic and milking in a little throttle while exercising some relaxation of the collective.

Ultrasport helicopter turbine conversion
The UltraSport helicopters rotor sheds energy reluctantly, but I was surprised at how well a little more throttle picked things up when it did. The 496 really has a sweet handling rotor, and if you don’t act like a total idiot, it will give you enough breathing room to recover from most common mistakes.
Just as important, the Hirth offers a very linear torque gradient that suits chopper flying very well. Many two-strokes have certain power ranges where rpm picks up too rapidly or creates sudden power “spikes”, making precise power control difficult, especially if those spikes occur in rpm ranges commonly used for some cruise configuration. The entire Hirth engine line seems to excel in this area. Power cuts in the 496 produce absolutely no negative or aggressive behaviour.
As a matter of fact, not a whole heck of a lot happens. Just counter the loss of power with corrective antitorque pedal, establish an additional 50 mph descent, and make sure that the first thing you do is get that collective “on the floor”. Initial rotor rpm degradation is modest, and there is actually a small period of time in which novice pilots might hesitate (though they certainly shouldn’t), but as long as they get the collective down to start a proper autorotation within a second or two, they will find that the rotor is more than willing to pick up lost energy readily. There is very little pitch change with a sudden power cut and the controllability of the aircraft suffers not at all.
Best autorotation speeds appear to be in the mid 50’s, although company procedure calls for about 45. I felt most comfortable with 50 to 55, and was rewarded with an easy transition to a landing flare. Since the aircraft was still in flight test at the time, all of our autorotation’s were done with power recovery, though I had absolutely no doubt that continuing to a full landing would have been easier than most other light piston helicopters… especially with that wide, wonderful, shock absorbing gear.
Two other things I noticed with the 496: The first is that one can wait well into the descent and select a more aggressive flare if circumstances warrant, or a more sedate/gradual flare/approach can be selected once one is familiar with the energy degradation characteristics of that rotor – and it doesn’t take long to get the feel of that puppy. One other note about this aircraft is that American Sportscopter seems to have struck an excellent balance between proper main rotor to tail boom clearance and tail boom to ground clearance.
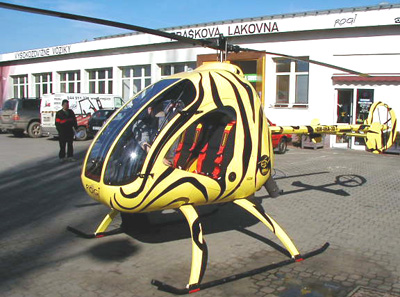
Hirth powered helicopter
Outside observation of several auto-rotations showed plenty of room for error between the rotor and tail boom on some aggressive “quick-stops”, as well as sufficient geometry to make slapping the ground with the tail boom a fairly rare possibility. I look forward to going back to American Sportscopter in the future and playing more with the autorotation characteristics of the 496, because what I saw I liked, and it was obvious that the machine was unusually forgiving in this regime.
Hovering auto-rotations were child’s play, and while I couldn’t do the 10′ high hovering autos that I did in the single-place aircraft, a 3-4′ hovering auto was a simple and surprisingly slow affair. Unlike a lot of light helicopters, the descent is a might slower than the norm, and a simple but steady recovery from 2-3′ means simply having to pull full up collective to cushion the landing and tap-dancing the anti-torque pedals to keep yourself heading in the right direction. Sweet.
I spent a fair amount of time in the 496 that day just manoeuvring aggressively, doing some high-banked S-turns along the ground, and through some traffic cones, as well as fast transitions between hover and forward flight, and a fair number of quick stops. Throughout all this abuse, I noted no overt sensitivity, no control impingements, and no untoward behaviour. Similarly, run-on landings were easily accomplished in the UltraSport helicopters so long as one let’s the Helicopter settle onto the gear slowly rather than trying to force it on. A very cool customer.
I flew the machine for approximately an hour and a half, made quite a few flights, and observed many more. Now in full production. I am looking forward to hearing reports from builders and pilots who will no doubt be having as much fun as I did. The character of this aircraft is forgiving, its handling was undemanding and while cruising a little slower than its competition; this machine excels in so many areas that it has to be given serious consideration by anyone who wants a Sport Helicopter that can carry a passenger.
One of the most positive aspects of this aircraft though, as I was flying along, was the reassuring feeling I had in knowing how it was engineered and constructed…and after what has happened to the Sport helicopter business in the last year or so, that is not a minor consideration. As I flew along in the 496, unlike certain other Sport helicopters that shall remain nameless (this time, anyway), I was surprised to note that I really wasn’t worried about the integrity of this aircraft.
Distributor – Australian dealer contact details: Helisport Australia
Manufacturer – Last known international dealer contact details: Advanced Technologies Inc.
PLEASE NOTE: American Sportscopters are no longer in existence and the Ultrasport 254 helicopter 331 and Ultrasport 496 helicopter are longer in production for public purchase. The design seems to have moved to military drone technology. A new design mimicking the original was floated recently online. A Google search may turn up some results on this machine.
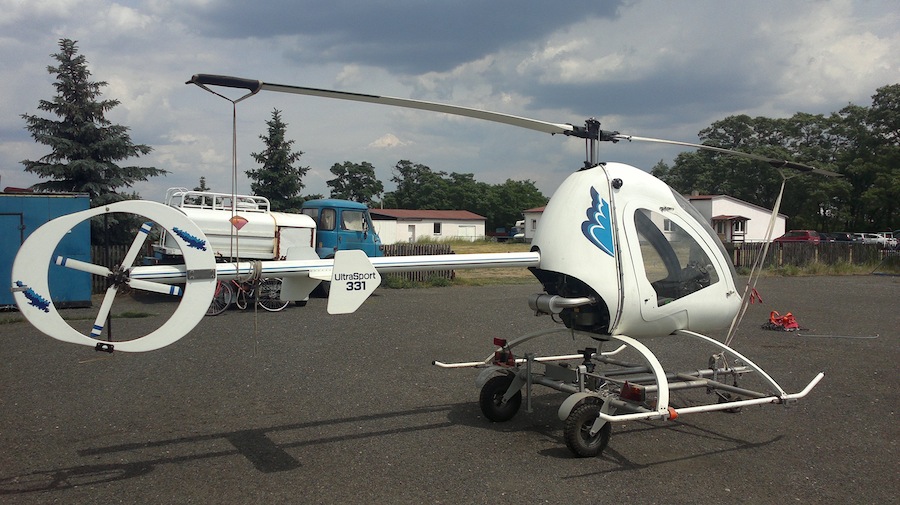
The company retrofitting the Ultrasport 496 helicopters with turbine engines, advanced FADEC ECU’s glass cockpit, automatic start sequencer, flight data recording and many more is the Cyprus based LAE Helicopters Cyprus.
Currently the company has moved to the next level to produce the Piranha helicopter.
More info in their website https://laehelicopterscyprus.com
Thank you for this updated information. It is extremely hard keeping up with how quick this industry moves and we ALWAYS appreciate the public helping us out with stories and information. Kind regards, Adam Aitken
Hello,
I’m looking for some parts of a Ultrasport 496: cabin, skids and main rotor. Do you know where I can find these components ?
Best regards,
Philippe
+33 666 911 747
Hopefully someone reading this might be able to help???
Hi, I might be able to find the parts you need. There are two Ultra Sport 496 helicopters sitting here in Guatemala, if you would like me to find if they will sell those parts I can do that for you?
Hello, I live in Panama and looking to put a 555T together. Looking for a good platform. I live in the Republic of Panama.
Thx
Looking for construction manual and drawings plus POH for the 254 or 331. I have two 254 kits. One is assembled.
Try contacting: http://www.vibrotech.com.au/331.htm and take a look at https://www.youtube.com/watch?v=1WErLvFpylg and also see if https://advancedtechnologiesinc.com/products-and-services/full-scale-models-and-mockups/uav-experimental-aircraft/ can help you.
HI, I have a Ultra Sport 496 which is in perfect shape, and I have another one that needs four tail rotor blades. I would apreciate if someone knows where I can buy them, please help. Mel Aparicio, 502-59579140 Guatemala City.