Engine RPM And Blade Pitch Management
While working in the RWI booth at Oshkosh a few years ago a real nice older gentleman and his friend came in and wanted to discuss designing their own helicopter. Their specific questions were geared mainly toward main rotor design and flight. After sitting with them for an hour or so I was intrigued with their enthusiasm but was concerned about their view on Rotorblade Pitch Management.
It was to be “fixed” pitch with altitude controlled by rpm only!!! They also wanted to take off straight up from their small driveway…yikes!!! I struggled to maintain myself and finally had to ask the question, “What if you loose engine power?” They both looked at each other and then said, “Oh, auto rotate like other helicopters, I guess.”
Needless to say after explaining basic helicopter aerodynamics and rotor systems theory they left scratching their heads contemplating how much re-design work they had ahead of them. However, I believe they also walked away with a much greater understanding and respect for rpm and pitch functions.
Engine RPM …what is it and why do we need it?
RPM or Revolutions-Per-Minute is a value necessary for a helicopter to produce enough lift so support itself. Most helicopters operate at around 450-500 rpm (higher for small homebuilt helicopters) for the main rotor and approximately a 5-6:1 ratio for the tail rotor or approximately 2250-3000 rpm. The main rotor rpm is typically shown in percent on a split or overlapping rpm gauge.

Rotorblade Pitch Management: A split overlapping RPM gauge useful for helicopter engine/rotor correlation
With the helicopter engine (Shown as “E”) and rotor (Shown as “R”) combined on top of each other or side by side. I have never seen a tail rotor rpm gauge in a helicopter, but I assume someone has installed one just to have yet another gauge to look at and reduce their useful load, sorry, just kidding.
Each variant of helicopter has its own specific rpm or rpm range that is optimal. We call this “Normal Operating” rpm. This range is usually shown on the gauge as green and at or above 100% rpm. It may also have a range of say 101 to 104%.
There are also rpm ranges on either side of normal which we call “Cautionary” which are usually yellow on your rpm gauge. This range is usually 90 to 97 – 101% on the low side and 104 to 110% on the high side. Each aircraft varies so don’t set these numbers in stone.
There may also be a separate yellow band, say 60 to 70%, which the pilot should avoid during warm up, spool up or spool down. This has nothing to do with the helicopter’s flight or “Ground Resonance”. It represents an area, which if maintained, could cause damage to the aircraft due to unwanted resonance or vibrations.
Finally, there are the “Don’t go there or you will die” rpm ranges beyond the cautionary flight portions. They are usually red and 110% on the high side and 90% on the low side of your rpm gauge. These two red lines have distinct and separate meanings. The upper red is “Over speed” and the lower red is “Blade Stall”.
An over speed is when the rpm is so great that the blades want to leave the rotor hub due to the super high centrifugal forces. Given enough time, usually only a few seconds, they will!!!
An “Under speed” or “Blade Stall” is when the pitch is too high to produce lift. This is usually initiated by exceeding MAP (Manifold Pressure) or torque due to the pilot dialling in too much collective. Ultimately resulting in rpm decay, so much so that the blades exceed their ability to produce lift and stall, no matter how much more power you apply.

Rotorblade Pitch Management: Managing engine power through a manifold pressure guage (MAP) on piston powered engines
Unlike the airplane, where given enough altitude, you can regain lift and continue to fly, you can stall the main rotors only ONCE with the helicopter.
As they stall they ultimately loose their ability to stay in plane and flap excessively. In forward flight the retreating blade usually dives since it stall first and the advancing blade rises.
This is known as “Blow Back”. As the helicopter starts to fall the added upward movement of air reacts on the bottom of the horizontal stabilizer causing the nose to dip.
Then the pilot applies aft cyclic aggravating the situation. The end result is usually chopping off the tail boom and….we you get the picture.
Not good…we’re a rock or lawn dart. A good saying to remember with the airplane is airspeed is life…with the helicopter rpm is life.
Ideally, your goal is to stay within the green area at all times. If you’re flying a governed ship this is done for you automatically. If you’re flying say the RotorWay, you need to monitor and adjust your rpm primarily with throttle and secondarily with collective, cyclic and even pedals.
Not super difficult, but one or more important things to be aware of as a pilot. I was actually fortunate to learn in the Robinson before they came out with a governor and I feel I am a better pilot because of it. Using all of the controls, especially the monkey motor of the throttle to vary rpm was, in my opinion, a bonus in my early training.
And remember, if you drift off into the yellow are now and then no big deal. Nothing is getting hurt mechanically. If you’re in the upper yellow you’re just wasting gas. However, if you’re in the lower yellow be aware that if your engine does go away or you have a ton of pitch dialled in you will have to react much, much faster with the collective then if it was in the green arc.
Especially with low inertia rotor systems. Also, don’t get complacent with a low rotor rpm horn or light if you have one. Always scan all of your gauges routinely. How would you ever know if your horn/light failed or not?
As a side note there are also different operating rpm ranges depending if you have power applied or not. And your rpm can change dramatically depending on G loading and /or cyclic movement. Finally, your tail rotor is directly affected by what your main rotor rpm is.
Beyond the normal ways to get into LTE or Loss of Tail rotor Effectiveness (remember the three main ones due to wind?)…just imagine how poorly your tail rotor is performing if you let the rpm droop.
Rotorblade Pitch Management: Pitch…what is it and why do we need it?

R22 with full left pedal
If managed correctly pitch can be our greatest friend. However, if left ignored it can bite real fast and hard. Generally we increase or decrease pitch with collective for the main rotors and pedals for the tail rotor. Main rotor pitch can also be varied with cyclic.
From a no wind hover to forward cruise flight the pitch between opposite rotor blades can go from equal to quite extreme. And from a low to high power setting in a hover, departure, or approach pitch can change dramatically. Realizing where your pitch is during all phases of flight is simply good situational awareness.
Many clues are constantly given to us through rpm, manifold, torque or engine gauges. The position of your collective is also obviously a real good indicator. And for non-governed ships, the throttle position adds much information.
One of my first high altitude flights to a logging area back in the Cascades of Washington State was an early eye opener for me. My poor little R22’s throttle was wide open and I had a ton of collective dialled in. Needless to say I knew right where the pitch was – very high while it was trying to grab as many air molecules as it could in order to sustain flight.
When given these types of situations it’s important to use a good deal of finesse. Smooth and small control inputs are required, there is no tolerance for any ego or macho flying, which could tip the scales into a possible blade stall.
So let’s look at just a few of many scenarios that could place your pitch into high angles of attack and cause blade stall.
Rotorblade Pitch Management: Approaches
Ideally you want to continue down a uniform shallow angle of about 15 degrees or less to your selected hover point. The closure rate should also be uniform from, say, your base to final airspeed of around 60 to 70 knots and then back to zero airspeed just as you arrive over the LZ (Landing Zone).
This allows for constant control and the ability to transition below ETL (Effective Translational Lift) way before your LZ. Ideally you want to know if your helicopter has the capability to HOGE (Hover – Out of Ground Effect) prior to reaching your LZ. That way you can abort the approach.
If you come in too fast and /or steep you risk having to grab a ton of collective right at the end of your approach. Resulting in increased pitch possibly beyond the helicopters ability to maintain HIGE (Hover – In Ground Effect).
The end result may simply be settling to the ground from only a few feet with no issues all the way to the worst case of falling to the ground due to blade staff without any real control and possibly rolling over.
Engine RPM And Rotorblade Pitch Management: Departures
As with the approach you want to depart up a uniform angle say around 15 degrees or less. And this angle usually starts just as you enter ETL. The key, as with the approach, is to slowly build airspeed from your hover point to normal cruise speed.
By doing this you never need to increase pitch while at low altitude. Remember, your goal is to minimize the pitch as much as possible and let the helicopter provide all the performance itself.
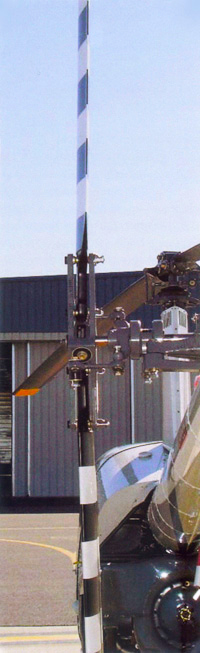
R22 with full right pedal
If you depart aggressively your pitch setting will be very high, your nose will be pointing down, and your reaction time to save the rotor rpm, (and the helicopter) given an engine failure, must be very quick.
Secondly, if your tail rotor fails during an aggressive departure you risk excessive yaw prior to being able to enter an autorotation to eliminate the high torque setting caused by the excessive pitch.
Rotorblade Pitch Management: Quick Stops
You might not have though this manoeuvre could cause any kind of pitch problem as you are merely loading the blades temporarily. During most upwind QS’s it shouldn’t. However, if by some chance you might need to do one downwind, the end result could be exciting to say the least.
First as you pull aft cyclic and reduce collective there is no real problem except the fact that you are now likely travelling within your own downwash.
Given the strength of the wind and speed of the helicopter you may also be below ETL, since the wind and helicopter may be travelling around the same speed together.
Then, as you level the ship and increase collective to complete the manoeuvre you may settle within your own downwash causing you to increase pitch further and possibly increasing the rate of decent – settling or rather falling to the ground.
Again, as with the approach, you could simply just settle to the surface without any consequence or possible impact the surface tail or nose first causing a “Hobby Horse” reaction and ultimately rolling over.
Engine RPM And Rotorblade Pitch Management: Normal and Hovering Auto
I think most of us know what would happen in either of these manoeuvres if we simply held the pitch in place as we lost power. Right…rpm’s toast and we’re a rock or lawn dart again in the normal auto and probably spread the gear and/or bend parts in the overing auto.
So, let’s look at the end of the normal helicopter autorotation and hovering auto as basically the same thing.
In the normal autorotation, at the end of the flare, we level the ship. In the hovering autorotation it’s already level.
In both cases the rpm and pitch should be about the same as we begin from skids level. The rpm could be higher at the end of the normal autorotation given build.
Remember, during the flare of the normal autorotation your rpm should have been increased to say 110% or red line due to Coriolis affect and your lowing of the collective.
However, when you pushed forward on the cyclic the rpm decreased possibly to the middle green area.
Now at the end of each of these manoeuvres you may hold or even lower the helicopters collective a little based on the blade inertia and rate of decent.
Timing of course is the key to pulling in a ton or collective at the right moment to cushion the set down.
Rotorblade Pitch Management & Timing
▣ If you pull too soon you risk blade stall and the outcome mentioned above with the gear and bent parts.
▣ Throw in too much forward momentum or lateral movement and we risk the rollover.
▣ Pulling too soon you also risk LTE since your rpm has dropped too much.
I hope this information has helped you to better understand the importance of rpm and pitch. Not only is it paramount to know what the ship’s rpm is at all times, it is equally important to know where the pitch settings are.
We’ve discussed some of the basic mechanics of the helicopter’s rpm and pitch systems and reviewed a few scenarios that could put us in harms way.
Hopefully this knowledge will aid in your quest to be a smarter and safer pilot.
Rotorblade Pitch Management: Autorotation by the numbers: R.A.T.S
▣ R – RPM – Adjust Collective
▣ A – AIRSPEED – Cyclic
▣ T – TRIM – Pedals
▣ S – SPOT – Watch
VIDEO: Robinson R22 Autorotation with Instruction

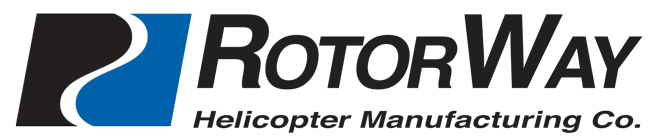
I am helicopter project