The concept of a ramjet-powered gyroplane was tried by the US Army many years ago, during their experiments with individual means of transporting ground troops relatively short distances. Several types of jet engines, including pressure jets, pulse jets and ram jets were tried.
These engines are not to be confused with what we now call jets — which are really turbines. An easy way to remember which is which is to repeat to yourself — turbines turn, and jets jet.
The most infamous pulse jet of all time was Hitler’s V-1 Buzz Bombs or World War 2 era. Most experienced modelers are familiar with another famous pulse jet — the Dynajet — which holds many speed records for model aircraft.
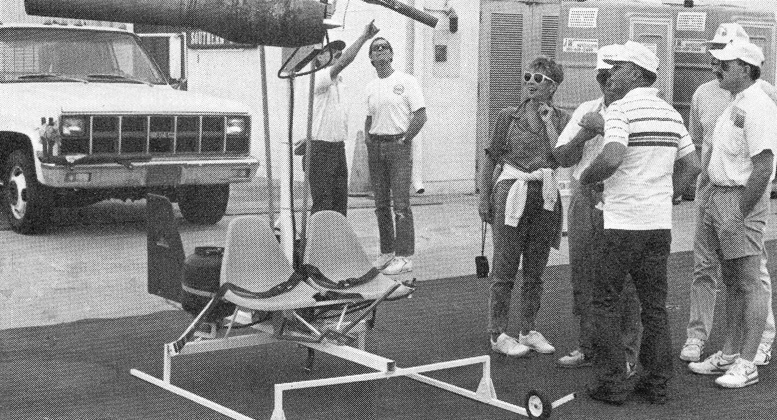
Spectators were really interested in this unique gyro. The very lightweight construction includes two plastic seats, thin square steel tube for the chassis and the bottles of propane behind the pilot. Will it fly? Owner claims it will.
A pulse jet engine works in spurts, or pulses, at very high frequencies per minute. In the pulse jet, as the gas exits, a petal valve opens, leaving a low-pressure area on the inside of the pipe. This forces the petals to open toward the inside of pipe, and this sucks another charge of gas into the pipe.
Residual flames ignite this charge and it explodes. The explosion forces the petal valves to close, leaving the burning gasses no way to go — but out the back of the pipe. The resulting forward pressure pushes the unit (and whatever vehicle to which it is attached) forward.
A very simple device, there are no moving parts on the pulse jet, with the exception of the stainless steel petal valve which flexes back and forth a fraction of an inch. However, because there is no fly-wheel effect with a pulse jet, any minor interruption of the fuel flow can cause a flame-out.
Some pulse jets are designed with a very complex fuel flow valve, and it is possible to control the top 15 percent of the power by controlling the amount of gas introduced into the engine. The second unit is a pressure jet which is usually propelled by fuel under “pressure”
The pressure jet is really a ram jet where the fuel is inserted under pressure into the combustion chamber. By doing this, it is not necessary to propel it through the air in order to feed the fuel to the engine.

Front view of the ram jet shows the fuel inlet supported by a tripod and a nose cone for dispersal of gas.
Either a fuel pump or propane is usually used’. In this type of jet, there are different stages of amplification of the burning gasses before they are routed into the main combustion chamber for exit out the tail pipe.
In a pressure jet, the amount of power can be controlled by a fuel valve. One of the most famous pressure jets is the Gluhareff, patented many years ago by Mr. E. M. Gluhareff for use in experimental one-man helicopters.
They have also been used in race cars, helicopters, a flying platform and several other applications. In both these units, the heat buildup in the tailpipe turns the metal white-hot, and this creates a definite fire-hazard in the vehicle being propelled.
The last of these jets is the ram jet which gets its power from gasses being introduced into the combustion chamber while the ram jet is in motion, thus the name. The outside air is rammed into the mouth of the tube, then a gas is introduced and ignited.
The hot gas then expands, and goes out the back of the tube, mixed with the air which is being forced in by the forward motion of the device. Ram jets are usually used in combination with some other means of forward motion. Any form of gas, including propane, can be used in a ram jet.
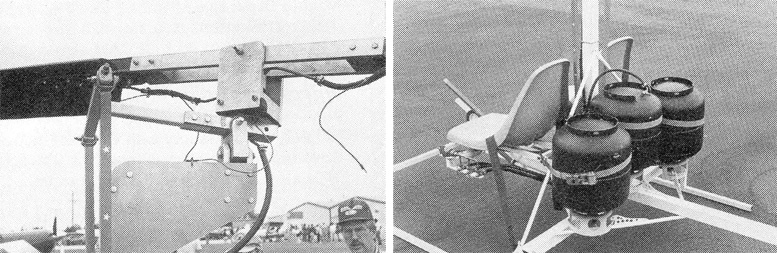
LEFT: The rotor head is a typical gyroplane with the exception of the electric wires for igniting the ram jet and the fuel lines.
RIGHT: Ram jets are powered by tanks of propane located behind the pilot. Ram jets are very fuel hungry.
When ram jets are used on the tips of rotor blades, the only torque resulting from this system would be that caused by friction in the rotor head bearings. Once underway, the airflow past the vertical stabilizer would keep the aircraft headed straight.
One problem which occurs with all of these jets is the necessity to carry a huge amount of fuel required for any sustained flight. Another formidable difficulty is the noise — it’s ear-shattering at best.
In spite of these drawbacks, it’s an accepted fact that these simple jets have fascinated homebuilders and experimenters for generations. This past weekend at the EAA Fly-In held at Camarillo, California, our contributing editor Glen Arthur found another version of the ram jet, and here’s his story:
A Tourque-less Rotor Ramjet Rotor Helicopter
In aircraft designs, there are two types of ideas — the conventional and the radical. Conventional designs incorporate the ideas which have always worked, then maybe, a few small changes are added for technical or aesthetic reasons.
The radical designs, however, caution is thrown to the winds in the quest to prove an idea, and looks be dammed. Given enough time, even a radical idea, if it’s sound, will become commonplace and conventional. If you’ve been to any EAA Fly-In lately, you’ve undoubtedly seen many examples of Burt Rutan’s once-revolutionary designs, so you know this is true.
The helicopter was once a very radical design too. It wasn’t all that long ago that the idea of rotary-wing flight was scoffed at as being an impossible dream. Nevertheless, through the years, that dream was not only realized, the helicopter even grew to become a dependable form of transportation.
As it was developed, the helicopter took on its own form of convention: Two rotors, a main lifting rotor and a tail anti-torque rotor, grew to be the norm. This conventional thinking worked very well, but there is always room for radical ideas to shake up the static ones and give people something new to think about.
This May, on Mothers’ Day weekend at the EAA Chapter 723’s Fly-In at Camarillo, California, we found a design which certainly made people stop, think and discuss. This machine looked very much like a helicopter but it seemed to be missing one thing — the engine.
Instead, this copter had, on the ends of the rotors, what looked like small buzz bomb motors and, in back of the two seats, on the small frame, there were three five-gallon propane cylinders. On closer inspection, the motors at the tips of the rotors were not the pulse jets of V-1 fame, but small ramjets fueled by propane.
It was a lot of fun watching people as they examined the craft, and listening as the “experts” expounded their views on the technology and theories of the unconventional helicopter, and then hearing them explain to anyone around why “that thing will never get off the ground!” When the builder, Mike Reed, finally turned up, he was bombarded on all sides with all sorts of questions.
It turns out that Mike purchased the plans for the craft from B.W. Rotor in Towanda, Kansas. Mike, who is a welder and contract plumber by trade, said that it took him about four months of “actual” time to build the copter.
He told us that it weighs 150 pounds dry, and that the kit designers claim will pull 300 pounds at 50 mph with a 100-mile range — a claim, Mike thinks, is very optimistic. The craft’s rotor was built by Mike with a laminated spruce spar and leading edge sheathed with airply.
The rotor head was machined from aluminum and is of the rigid rotor type. The three propane cylinders feed into a control manifold and an “All” valve which controls the flow of liquid propane to the motors.
Mike says that the motors have been run up, but the nozzles were too large, and so allowed the motors to burn too rich. Ramjets work best when all the fuel is burned within the cylinders, and Mike said that the nozzles supplied in the kit let a good portion of the combustion occur out of the back end of the motor.
Mike has modified the nozzles by cutting down the flow by one-half, but has not yet run the new nozzles in the motors. Mike reported that the motors are rated at 20 pounds of static thrust, and really spin the rotor up. He doesn’t have any rotor rpm figures yet, but will get them with the new motors.
To start the motors, you first flood the – cylinders with propane gas, then ignite them with the spark plugs in the motors, using a Phizeo-electric source (like the automatic pilot light in most new gas appliances).
You then let the motors warm up for a couple of minutes then, when the motors are warm, you turn on the liquid propane. By this time, the rotors are already spinning at a good rate, and the noise, as Mike admits, is a low roar — similar to that put out by a roofer’s tar pot heating up.
Mike is thinking about using small turbojets instead of the ram jets in a later model, and is putting several of his ideas on the subject down on the drawing board.
When Mike was asked by several bystanders if he were actually going to fly his ram-jet copter, Mike smiled and said, “Yes — eventually” Well, Mike, we wish you the best of luck. Let us know how it turns out.
HILLER HORNET
A Diminutive Two-Seater Ramjet Helicopter : Low Operating and Initial Costs: Military Possibilities
SINCE 1948, when he succeeded in marketing a reliable and economical light helicopter — the Model 360 — Mr. Stanley Hiller has been recognized as a brilliant young designer (he is a 26-ycar-old Californian) who has something to show to many of the old hands. He has now announced successful flights with a new design named the Hornet.
It is a small two-seater with ramjet (athodyd) propulsion at the blade-tips. It seems that investigation of the costs of the Hiller 360 indicated that the most expensive units were the transmission, gearing and clutch, and, of course, the engine itself.
A way of eliminating them all was to employ ramjets; many possible designs were therefore studied and eventually a type was developed which could do the job for a consumption of 41 gal/hr for the two units—one on each blade-tip. Research continues, and later units give hope of eventually halving this consumption figure.
Two of the three Hornets now flying. One is seen in skeleton form, the other complete with plastic skinning ond Plexiglas Cabin enclosure.
The existing ramjets are simple and light and require virtually no servicing. They are not particular as to the type of liquid fuel fed to them, though kerosene or high-octane petrol give the best results. In order to light up it is necessary to accelerate the rotors to a minimum of 150 r.p.m., and three alternative design arrangements have been devised for the purpose.
The rotor may be hand-cranked, or turned by a portable electric motor with battery, or rotated by a small two-stroke petrol engine (described as of the motor-mower type but better explained, perhaps, as an “inboard outboard” built into the aircraft.
When the rotor has attained 150 r.p.m., fuel pressure is built up with the aid of a wobble pump in the cockpit and the fuel-flow valves are then opened. On the starter button being pressed the jets fire, and the r.p.m. start to build-up rapidly.
The starting procedure takes about 1 ½ mins and operational rotor speed is 500 r.p.m. Presumably centrifugal force produces the requisite fuel-feed pressure once the blades are turning under power.
The ramjets, which have no moving parts, are constructed from heat-resisting steel, and they are attached to the blade tips by two bolts and a steel support. Replacement of a unit is said to take only 3 min. The equivalent power of the two ramjets is 70 h.p., or in terms of thrust they produce 30 lb each.
Highest operating temperatures are in the region of 3,000 deg F., and the life of the present units is given as 500 hours. At the operational rotor speed of 500 r.p.m. the tip speed is approximately 450 m.p.h.
HILLER HORNET: Dimensions and Performance | |
---|---|
Fuselage length | 12ft 8in |
Track | 5ft |
Height | 6ft 8in |
Rotor diameter | 23ft |
Empty weight | 340 lb |
Disposable load | 560 lb |
Gross weight | 900 lb |
Maximum speed | 85 m.p.h. |
Cruising speed | 70 m.p.h. |
Climb | 1,200ft/min |
Estimated ceiling | 12,000ft |
Range (30 Imp. gal) | 50 miles |
Endurance (30 Imp. gal) | 40 min |
As more efficient ramjets are developed it will be a very simple matter to replace the earlier type on the machine. With only limited production in mind, a price of 200 dollars per unit has been mentioned, but in the event of large-scale production being ordered a much lower price could be expected.
By comparison with the weight of a piston engine to produce the same power, the weight of the ramjets—11 lb each— is remarkable. It is, in fact, the reduction in weight of power unit and transmission which has enabled the empty weight of the Hornet to be kept to little more than a third of the all-up-weight of 900 lb.
Incidental advantages claimed for the Hornet’s ramjet power source are best listed as negatives: no carburetor to ice up; no ignition system to fail or require maintenance; no radio interference; no warming-up delays; and practically no general maintenance.
Regarding noise, it is understood that in flight the level compares with that of the Model 360’s 200 h.p. piston engine, but that when the machine is hovering it is somewhat louder.
Turning to the Hornet’s controls and airframe, like the earlier 360 it has an overhead cyclic-control stick and rotor-matic controls.
Replaceable in three minutes, and provisionally priced at 200 dollars, the Hornet’s tiny ramjets weigh 11 lb and produce 30-lb thrust.
This stick governs the direction of flight. Another manual lever looks after collective pitch and incorporates a power control—in this case a fuel-flow valve. This one is concerned with “up and down” flight or, if moved from side to side, operates the rudder to control the heading of the aircraft. These are the only two controls.
The rotor blades comprise a solid extruded aluminium alloy leading-edge and a built-up trailing portion of magnesium alloy. The fuselage of the Hornet could scarcely be simpler. It consists of a two-seat enclosed cabin and a tail boom, both constructed from tubular steel and covered with plastic material.
The front of the cabin comprises two very large Plexiglas panels and their frames. In addition to the control levers the cabin contains a wobble pump, a starting button, a fuel-flow gauge, a rotor r.p.m. indicator, an A.S.I. and an altimeter.
It is learned from C.B. Helicopter Hire, Ltd. (of School Lane, Chearsley, Aylesbury, Bucks), United Kingdom joint representatives for Hiller Helicopters, Inc., that plans were in hand to market the Hornet commercially in large numbers, beginning this spring, and that a target price of 4,900 dollars had been in mind.
The present international situation, however, has dictated that the resources of the Hiller factory be devoted entirely to Service production of the type 360. The first order for a trainer version of this aircraft was placed by the U.S. Navy, but a later Army order for ambulance 360s was given priority in view of the urgent requirement in Korea.
In addition, a U.S. Navy contract has been awarded to Hillers for the development of jet rotor designs (Flighty January 11th). The initial batch of 12 Hornets—three of which are flying, while the components of the remainder have been completed—may therefore be the only one for the time being.
An extensive test and development programme is in mind for them. There is little doubt that with a price of about £1,000, controls (two only) which are easy to handle, and an aircraft which is inherently stable, the Hiller Hornet approaches nearer than any other to the conception of an “everyman” helicopter.
Should military authorities see a future for these remark able little machines—as seems possible—and place a sizeable order for them, they might ultimately become available for much the same price as a light car. It is by no means fantastic to foresee helicopter despatch-riders with machines rugged and simple enough to be maintained in an M.T. section.
From the civil point of view, where the cost of the helicopter has so far been a major snag, not only is the price provisionally proposed for the Hornet well within the means of thousands of private owners, but running costs, and in particular maintenance and repair (and therefore, no doubt, insurance too) may possibly be kept lower than those of a two-seater fixed-wing aircraft.





Hi Dears : Did You know a extruded bar saler in US
Thank You.
https://www.aircraftspruce.com/
I saw the Hiller Hornet in person this week at the Hiller Museum. Really neat piece of equipment and you can easily see how much simpler the total design was compared to other helicopter designs.