Commercial Helicopter Comfort
What price an engine change? When the Bell 222 developed a reputation for poor powerplant reliability, the Canadian manufacturer switched from Lycoming to Allison, raised maximum all-up weight and redesigned the cowlings improving looks as well as access.
ARTICLE DATE: October 1993
The first question to answer is why the Bell 230 Helicopter? At a quick glance the 230 looks almost identical to its predecessor the Bell 222 first introduced in 1980 – a very attractively styled helicopter in the medium capacity range. With awesome firepower, speed and manoeuvrability, all seeing sensors and “Whisper Mode” it was the star of Air wolf.
In real life the Treble Two was a capable helicopter with unusual natural stability enabling it to be certificated by the FAA for single pilot IFR flight without the addition of an autopilot. The Achilles Heel of the aircraft were the Lycoming LTS 101 engines which acquired a reputation for maintenance difficulties.
As with most such reputations, like the rust prone-ness of certain Italian cars, the rumor was worse than the reality. Once acquired – very difficult to change, so the Lycomings had to go. They were replaced by the Allison 250 C30 G/2s.
It must be said that the C30s didn’t have an unblemished reputation when first fitted to the Sikorsky S76, but they have matured into engines noted for their reliability and fuel efficiency over hundreds of thousands of hours of operation.
All the other changes are less obvious but start with structural strengthening allowing an increased MAUW of 8,400 lbs and changes suggested by servicing experience. Bearings have been uprated, seals improved to reduce seepage and, importantly, the cowlings enclosing the engine and transmission have been redesigned.
This had three aims: to improve accessibility, to improve the airflow characteristics through the engines and to increase the airflow through the engine bay, reducing temperature enhancing engine reliability.
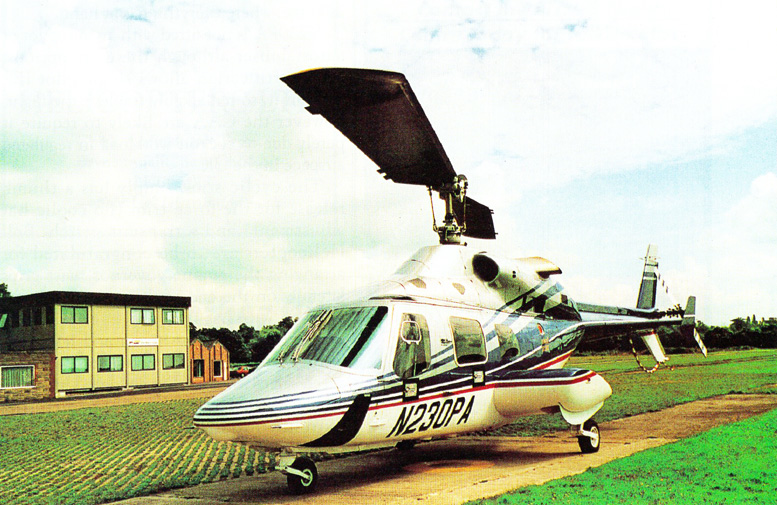
OPERATORS OF THE BELL 230 helicopter have the option of wheel or skid landing gears. While retractable wheels avoid downwash effects during taxiing, the lighter skids permit the loading of an additional 222 litres of fuel.
A side effect is more aesthetically pleasing lines through the elimination of unsightly holes and screens. Additionally several of the internal access arrangements have been improved to ease the engineer’s task.
The Bell 230 Helicopter rotor system has two decidedly beefy looking blades with steel spars and fibreglass straps for structural redundancy. Blade chord is a massive 2’2″ with swept tips to reduce rotor noise, although a distinctive “beat” can still be heard at some distance when the helicopter is approaching at cruise speed.
This is one area that the Bell 430 model with a four-bladed rotor system is set to address. At first sight the rotor head appears to have the conventional Bell teetering hinge system but on the 222/230 the hinges are elastomeric (flexible), giving greater equivalent hinge offset and hence greater control power – the elastomerics have been further improved in the 230.
The fuselage is suspended from the main gearbox by the Bell patented Nodal Beam system first seen in the LongRanger. The attachments to the fuselage are at the points of nil vertical vibration of the beam.
In the Bell 230 Helicopter it is possible to fine tune the attachments for the individual aircraft. All this effort is necessary because of the inherent “two per rev” vertical vibration common to two-bladed rotor systems.
Vibration is further reduced by two Frahm dampers, one in the nose to absorb yaw vibrations and the second in a stub wing to damp vertical movement. Frahm dampers are rigid pendulum devices tuned to a particular frequency. Operators have the choice of wheel or skid undercarriages.
Corporate operators will almost certainly opt for the flexibility of the retractable wheeled gear avoiding the effects of downwash when taxiing. More utilitarian users will probably opt for the less complicated skid system which saves 89 lbs and allows for an additional 223 liters of fuel in the stub wings.
The passenger cabin can be configured in a variety of ways – from utility eight seat to a luxurious four-place VIP interior. As the aircraft can be flown single pilot an additional passenger can be carried in the left cockpit seat.
The options list runs the whole gamut from auxiliary 48 gallon fuel tank to custom interiors, acoustic insulation, inlet particle separators, cargo hook and a wide range of high tech navaids. If you want it you can have it – at a price.
A typical IFR equipped Bell 230 Helicopter with all CAA mandatory mods, retractable undercarriage, custom deluxe six-place cabin, auxiliary tank, co-pilot controls and instruments and emergency floats would set you back $4,298,200 plus delivery. Ouch!
However, this buys you a helicopter capable of cruising at 140 kts with a potenial maximum range of 340 nm with reserves, in some comfort, which is a pretty impressive capability.
Our subject, a factory demonstrator, is ship seven off the production line. It was kindly made available to us by Alan Mann helicopters Ltd at Fairoaks who are Bell helicopters’ sole UK distributors and will be exhibiting the aircraft at Helitech.
We were hosted by Gary Savage. He has a justifiable enthusiasm for the product and fielded our endless questions with great good humor, hardly even flinching as we formatted for the photo shoot.
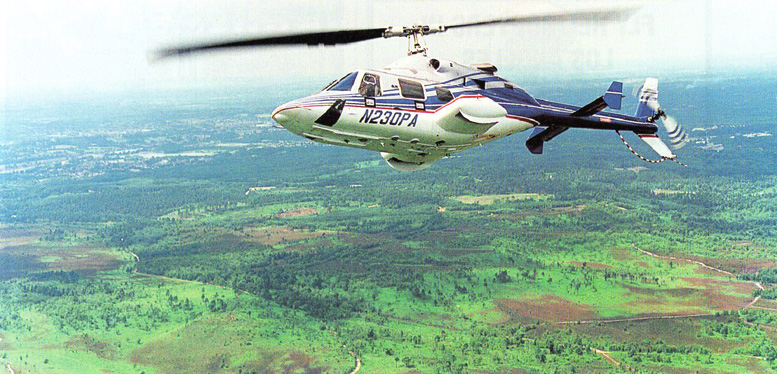
BELL HELICOPTER has redesigned the 222’s engine cowling for the 230, with the aim of improving powerplant accessibility, airflow characteristics through the engine and airflow through the engine bay.
The Bell 230 Helicopter demonstrator is comprehensively equipped with full dual controls, leather Radar, GPS, Environmental Control System (ECS), six-seat club cabin upholstered in soft silver grey leather.
The cabin has large windows and in this configuration is spacious and pleasing to the eye. Even the door locking system is obvious and smooth unlike the majority of larger helicopter doors which are unreasonably difficult to operate.
T h e cockpit shows every sign of being designed with pilots’ opinions in mind – the seats are actually comfortable! They can be adjusted in all directions, although fore and aft “notches” are rather coarsely spaced. They demand care on latching.
Yaw pedals adjust smoothly by turning a knob on the center pedestal; it was rather nice not to have to grovel under the panel. Yippee – I didn’t need a cushion in this one and tall constant companion had no complaints either.
Mounted in the Bell 230 Helicopter instrument cowl above the panel are grouped the avionics selectors, in comfortable line of sight where you want them (though strangely the station boxes were remote on the pedestal).
A continuous double strip of captions form the central warning system at the top of the instrument panel. Some of the colors will be changed for UK registered aircraft (generator warnings should be red for instance).
The flight instruments include EFIS attitude indicators and HSIs with analogue/digital altimeters and electronic VSIs. Navigational information from the navaids can be superimposed on the HSI.
The rpm and torque gauges are to the left of the flight instruments. TQ gauge has the single upper needle registering rotor mast torque (normally used), with the two individual engine torques below used when in the “one engine inoperative” (OEI) mode.
Engine and system gauges are grouped conventionally in the center. It is a cockpit in which you feel at home, where everything is at hand. N230PA is not fitted with an autopilot or auto-stabiliser although these are options.
FAA certification allows single-pilot IFR without it, so remarkably stable is the flight, however the CAA are likely to require it purely due to cockpit workload in regulated airspace in the UK.
The Bell 230 Helicopter cyclic stick simply has a thumb release for the force trim (no coolie hat adjustment) and a transmit switch. Bell Helicopters are to be congratulated for arranging the engine governor twist grips laterally on the end of the collective lever.
Anyone who has flown an approach with one engine governor frozen and left hand flitting between collective and roof mounted speed select lever will be delighted with this arrangement. The collective box also carries switches for the idle stops, rpm beep trims/torque matching and landing light controls. There is no nosewheel lock.
Take-off weight for this sortie was 7915 lbs, 485 lbs below MAUW. This aircraft has 770 lbs of optional equipment fitted which makes something of a dent in the available payload. With three POB, full main and auxiliary fuel there would be payload available for two more passengers and 145 lbs or so of baggage.
Under these conditions, cruising at 6000ft TAS should be 140 kts and range with 20 minutes reserve would be 350 nm. However, if all six cabin seats were occupied with standard passengers and no baggage, fuel load would have to be reduced to 1400 lbs – range coming down to 280 nm.
Anyway, let’s get started. All the systems controls are in the front roof console, nicely angled for viewing by even elderly eyes. The selected engine prime switch is depressed and then the starter button.
As N1 rpm comes up to 13%, the appropriate twist grip is rotated, modulating fuel flow to keep the MGT peaking at about 800°C. At 58% N1 start is completed, prime switched off and the rotor is turning. Engine starting is from the internal 28ah battery.
When the generator charge rate has reduced the second engine is started. There are two separate electrical systems. Failure of one requires manual selection to interconnect to the other system.
There are also two entirely separate hydraulics systems, each of which will maintain full system functions with the exception of the tail rotor boost which is only operated by the No 1 system. Hydraulics selectors will probably move to the collective in UK aircraft. Twin inverters are also brought on line by switches in the roof console.
Bell quote 60 kts as a rotor start wind limit, for an onshore day this sounds fairly unpleasant. Today with just a few knots there is no evidence of blade sailing with this head design.
With all systems on line and functional checks complete, rotor rpm are brought up to 100 per cent and torques matched with lateral movement of the beep switch. The ECS is switched on and very quickly lowers cockpit and cabin temperatures to comfort level in the bright sunshine but at some cost in increased noise level.
Lift off to the hover is a 1-2-3 process; nosewheel first then right then left wheels. Hover attitude is left wheel low and about 10° nose up. There is still good vision over the cowl and the ground can be seen quite close in to the aircraft.
The Bell 230 Helicopter chin windows are small and not really used for normal hover reference. In the hover we seemed to be using 75% torque with MGTs at 660°/630°. Spot turns in the hover were no problem in the light wind, with plenty of tail rotor authority and just a slight tendency for the rate of turn to increase in right turns.
On the take-off, critical decision point (CDP) at 40 kts/40ft is quickly reached and best rate of climb achieved at 70 kts. The Bell 230 already feels very stable and in fact the first impression is of a much bigger aircraft. The cyclic control is very positive and large roll rates can be achieved very easily.
Yaw pedals are if anything slightly too light and sensitive but after a short while it becomes apparent that the required movement for balanced flight is only about an inch between cruise and descent powers. As we level off at 2000ft 90% torque is selected and the speed builds up to an observed 143 kts, in today’s conditions this equates to 147 kts TAS.
Vibration level is low but rather hard to analyze. It is definitely not the obvious two per rev bounce but a slight background vibration felt rather more obviously through the floor in the rear cabin.
Noise level is a sort of low roar, fairly quiet for a helicopter, both in cockpit and cabin, but more comfortable with headsets on. If real peace and quiet is required, an optional acoustic reduction fit can be specified – at a cost of course – with a weight penalty of 103 lbs.
Although there is no coolie hat adjustment for the force trim it is easy to trim the helicopter for level flight. 10 kt disturbances to the speed seem to damp out after two or three long gentle oscillations, showing that dynamic stability is positive in pitch.
There is a slight tendency to wander in roll but overall the Bell 230 Helicopter can be left to its own devices for quite long periods, proving that an autopilot would be a luxury except in very high cockpit workload conditions.
Inside the aircraft there is very little evidence of a characteristic blade slapping sound even in quite positive high speed turns. In the usual 60 to 80 kt blade slap region in the descent, it is necessary to open the cockpit window to hear it.
As you still can’t get Whisper Mode, consideration for those on the ground suggests a better descent technique is to keep the speed up and then reduce speed positively later in the approach.
With the force trim switched off the cyclic feel is just like a JetRanger, ie; virtually forceless, but the effectiveness of the control is unlike any JetRanger. There is none of the “move the stick and then bring it halfway back again” technique of normal two bladed types.
If anything, it is easier to fly manoeuvres with the force trim out, in contrast to the Sikorsky S76 which can be quite a challenge. Overall, it is a benign helicopter from the pilot’s point of view.
The next thing on the agenda is a single engine approach. No 1 twist grip is brought back to split the needles. In single engines condition, 86% torque is the maximum allowable for training purposes and this results in a IAS of 115 kts at our weight.
In a real OEI situation, 97 – 100% torque is allowable for 2.5 minutes and 86.4 – 97% for 30 minutes giving ample power for dealing with the critical case of engine failure just after CDP. As the No2 engine takes over RRPM are beeped up slightly to 100%.
The approach is flown normally and being limited to 86% single engine torque, a very slow running landing is carried out making sure that the hover attitude is adopted 10 to 15ft above the ground to prevent tail scrapes.
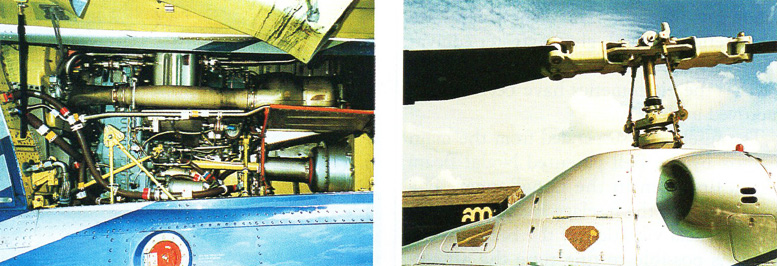
REDESIGNED ENGINE COWLINGS are intended to improve access as well as airflow for cooling the engine bay. The Bell 230’s teetering hinges are elastomeric, improving control power.
At a later point during the Bell 230 Helicopter photo shoot, formation with the Bell 206 camera aircraft showed that the stability and general ease of control was not just a first impression.
It was truly the easiest helicopter that Derek with his considerable experience on different types had ever flown in formation. What do we think of the Bell 230? It appears to be aimed in the UK mainly at the corporate and police and EMS markets.
Seeming rather small for offshore, it doesn’t have the ultimate cabin space of the Sikorsky S76. Perhaps more realistically the Bell 230 is the next step up for organizations currently operating Aerospatiale Twin Squirrels or Agusta 109s.
This niche in the market would appear to be rather a narrow one. The Bell 230 Helicopter cabin is comfortable and can be specified with a very luxurious interior indeed although over enthusiasm in this area can lead to significant reductions in range.
Bell Helicopter Textron have introduced a support plan for the Model 230 for a fixed cost per hour, to include pilot and engineer conversions, special tools, spare parts and line replacement units for all maintenance. Undoubtedly a boon to the Aviation Manager wishing to accurately budget for the cost of operation.
From a purely selfish pilot’s point of view, the cockpit is one of the best we have come across in helicopters as a place to go to work in and the aircraft achieves an ease of handling without artificial aids that is rare. Very impressive; can we have one for Christmas please?
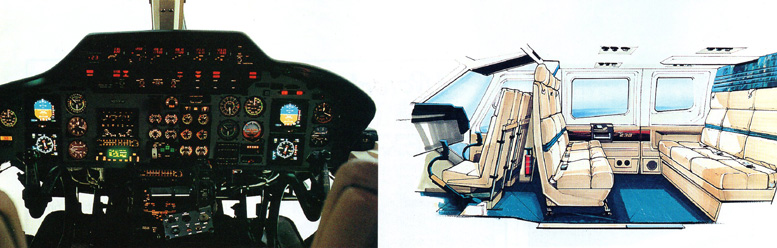
LEFT: THE COCKPIT appears to have been designed with pilots in mind. Avionics selectors are mounted in the cowl above the panel with central warning captions below.
RIGHT: THE PASSENGER CABIN can be configured in several ways, from utility eight-seat to luxury four-seat lay out, with another person in the front left seat.
Bell 230 Helicopter Specifications | |
---|---|
BELL 230 HELICOPTER DIMENSIONS | |
Fuselage Length | 42’6.8" |
Rotor Diameter | 42" |
Overall Length, rotors turning | 50’5.5" |
Height | 12′ |
Width | 11’4" |
Passenger Cabin Length | 6’3" |
Cabin Width at elbow level | 410" |
Baggage Locker Volume | 43.2 cu’ |
BELL 230 HELICOPTER WEIGHTS AND LOADINGS | |
MAUW | 8400 lbs |
Empty Weight – basic configuration on wheels | 5045 lbs |
Max Useful Load | 3335 lbs |
Max Normal Fuel Weight | 1255 lbs |
Aux Tank Fuel Weight | 322 lbs |
Empty Weight, as tested | 5816 lbs |
BELL 230 HELICOPTER PERFORMANCE | |
VNE | 150 kts |
Max Sea Level Continuous Cruise at MAUW | 137 kts |
Increasing at 7000 AUW | 142 kts |
Max Range SL, MAUW, long range cruise, 134 kts, no reserve | 379 nm |
Max ROC, twin engine | 1530 fpm |
Max ROC, single engine | 735 fpm |
ISA Hover Ceiling IGE at MAUW | 12,300ft |
ISA Hover Ceiling OGE at MAUW | 7,300ft |
ISA Service Ceiling, single engine at MAUW | 8,500ft |
BELL 230 HELICOPTER ENGINES | |
Two Allison 250-C30G/2 Twin engine TO Power (5 min) | 700 SHP |
Max Continuous | 622 SHP |
Single Engine (2.5 min) | 779 SHP |
Max 30 min Power | 742 SHP |
Transmission Ratings Twin Engine TO (5 min) | 925 SHP |
Max continuous | 875 SHP |
Single Engine Max Continuous | 735 SHP |
BELL 230 HELICOPTER MANUFACTURER | |
Company | Bell Helicopter Textron Canada Limited |
Price (1993) | Budgetary price, ex factory, standard aircraft incorporating CAA mandatory modifications US$3,640,000 |





Be the first to comment on "The Bell 230 Helicopter – A Most Comfortable Office"